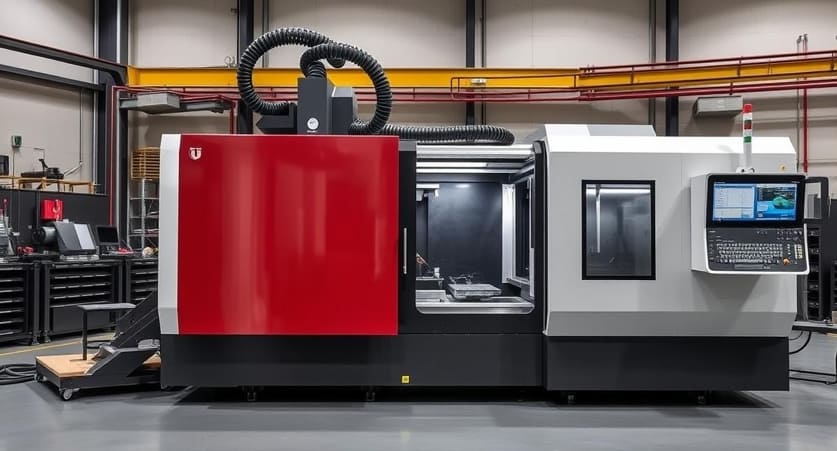
Aluminum is a versatile and widely used material in various industries due to its lightweight, durability, and excellent machinability. It is often the go-to choice for aerospace, automotive, and electronics components, among others. However, not all machining centers are equally adept at handling aluminum. In this article, I’ll share my knowledge and insights on the types of machining centers that are best suited for aluminum and why. We’ll also explore some frequently asked questions and tips to ensure you get the best results when machining this material.
Why Aluminum is a Popular Choice for Machining
Before diving into the specifics of machining centers, let’s take a moment to understand why aluminum is so popular. Here are a few key reasons:
- Lightweight and Strong: Aluminum is much lighter than steel but still offers good strength-to-weight ratio, making it ideal for applications where weight is a critical factor.
- Corrosion Resistance: Aluminum naturally forms an oxide layer that protects it from corrosion, which is particularly useful in marine and outdoor applications.
- Thermal Conductivity: Its high thermal conductivity makes it excellent for heat sinks and other thermal management components.
- Ease of Machining: Aluminum is relatively easy to machine, which reduces production costs and time.
- Recyclable: Aluminum is 100% recyclable, making it an eco-friendly choice.
Types of Machining Centers Suitable for Aluminum
High-Speed Machining Centers
High-speed machining (HSM) centers are designed to operate at incredibly fast spindle speeds, often exceeding 15,000 RPM. These centers are particularly well-suited for aluminum because:
- Increased Productivity: The high spindle speed allows for faster material removal, reducing cycle times and increasing productivity.
- Improved Surface Finish: High-speed cutting results in smoother surface finishes, often eliminating the need for secondary operations.
- Better Tool Life: The reduced cutting forces and heat generation in HSM can extend the life of cutting tools.
Multi-Axis Machining Centers
Multi-axis machining centers, such as 5-axis machines, offer unparalleled flexibility and precision. They are ideal for complex aluminum parts that require intricate designs and tight tolerances. Here’s why:
- Complex Geometry: Multi-axis machines can handle parts with complex geometries, such as those found in aerospace and medical applications.
- Single Setup: The ability to machine from multiple angles in a single setup reduces the risk of alignment errors and improves accuracy.
- Efficient Machining: They can machine multiple features simultaneously, reducing the overall machining time.
Bridge Mills
Bridge mills, also known as gantry mills, are large-scale machining centers that are perfect for machining large aluminum components. They are often used in the aerospace industry for parts like aircraft wings and fuselage sections.
- Large Work Envelope: Bridge mills can accommodate large workpieces, making them ideal for large-scale projects.
- Stability: The robust structure of bridge mills ensures stability and precision, even when machining large and heavy parts.
- Customization: Many bridge mills come with customizable options, allowing you to tailor the machine to your specific needs.
Vertical Machining Centers
Vertical machining centers (VMCs) are the most common type of CNC machining center. They are versatile and can handle a wide range of aluminum parts, from small components to larger ones.
- Cost-Effective: VMCs are generally more affordable than other types of machining centers, making them a popular choice for small to medium-sized businesses.
- Ease of Operation: The vertical orientation of the spindle makes it easier to load and unload parts, improving workflow efficiency.
- Wide Range of Applications: VMCs are suitable for a variety of applications, including milling, drilling, and tapping.
Horizontal Machining Centers
Horizontal machining centers (HMCs) are designed for high-volume production and are particularly useful for machining large and heavy aluminum parts. They offer several advantages:
- Heavy-Duty Capabilities: HMCs can handle larger and heavier parts with ease, making them ideal for automotive and heavy machinery components.
- Chip Evacuation: The horizontal orientation of the spindle facilitates better chip evacuation, reducing the risk of tool damage and improving surface finish.
- Automated Loading: Many HMCs come with automated pallet changers, which can significantly increase production efficiency.
Factors to Consider When Choosing a Machining Center for Aluminum
Spindle Speed
Aluminum requires high spindle speeds to achieve optimal cutting performance. A machine with a spindle speed of at least 12,000 RPM is recommended, but higher speeds (up to 20,000 RPM or more) are even better.
Tooling
Using the right tools is crucial for efficient aluminum machining. Carbide tools with sharp edges and high rake angles are typically the best choice. These tools can handle the high speeds and provide a better surface finish.
Coolant System
Aluminum machining generates a lot of heat, which can lead to tool wear and part distortion. A robust coolant system is essential to keep the cutting area cool and remove chips effectively.
Rigidity and Stability
The machining center should be rigid and stable to maintain accuracy and surface finish, especially when machining large or complex parts. Look for machines with a solid cast iron or granite base.
Automation Capabilities
For high-volume production, consider machines with automation capabilities such as pallet changers, robotic loaders, and automatic tool changers. These features can significantly boost productivity and reduce labor costs.
Comparison of Machining Centers for Aluminum
To help you make an informed decision, here’s a comparison of the different types of machining centers suitable for aluminum:
Type of Machining Center | Key Features | Best Suited For | Advantages | Disadvantages |
---|---|---|---|---|
High-Speed Machining Centers | High spindle speeds (15,000+ RPM), rapid feed rates | Small to medium parts, high-precision applications | Increased productivity, improved surface finish, better tool life | Higher initial cost, requires specialized training |
Multi-Axis Machining Centers | 5-axis or more, simultaneous multi-directional machining | Complex parts, aerospace, medical applications | Handles complex geometries, single setup, efficient machining | Higher complexity, more expensive, requires skilled operators |
Bridge Mills | Large work envelope, robust structure | Large parts, heavy components, aerospace applications | Accommodates large workpieces, stable and precise, customizable | High cost, large footprint, specialized maintenance |
Vertical Machining Centers | Vertical spindle, wide range of applications | Small to medium parts, general machining | Cost-effective, easy to operate, versatile | Limited to vertical machining, less efficient for large parts |
Horizontal Machining Centers | Horizontal spindle, heavy-duty capabilities | Large and heavy parts, high-volume production | Handles heavy parts, good chip evacuation, automated loading | Higher cost, complex setup, larger footprint |
Tips for Machining Aluminum
1. Choose the Right Cutting Tool
- Material: Carbide tools are the best choice for aluminum due to their hardness and ability to maintain a sharp edge.
- Geometry: Tools with high rake angles and sharp edges are essential for achieving a good surface finish and reducing cutting forces.
2. Optimize Cutting Parameters
- Speed: Use high spindle speeds to achieve optimal cutting performance.
- Feed Rate: Adjust the feed rate to balance productivity and tool life.
- Depth of Cut: Use shallow depths of cut to minimize the risk of part distortion and tool wear.
3. Use a Suitable Coolant
- Type: Water-soluble coolants are generally preferred for aluminum machining as they provide excellent cooling and lubrication.
- Flow: Ensure a consistent and adequate flow of coolant to the cutting area to remove heat and chips.
4. Maintain the Machine
- Regular Checks: Regularly inspect the machine for wear and tear, especially the spindle and tool holders.
- Cleaning: Keep the machine and cutting area clean to prevent chip buildup and ensure consistent performance.
5. Consider Workholding Solutions
- Clamps and Vises: Use high-quality clamps and vises to secure the part firmly without causing damage.
- Fixtures: Custom fixtures can be used for complex parts to ensure accurate and repeatable results.
FAQs
1. What is the best machining center for small aluminum parts?
Answer: For small aluminum parts, a vertical machining center (VMC) is often the best choice. VMCs are versatile, cost-effective, and easy to operate, making them ideal for a wide range of small to medium parts.
2. Why is high spindle speed important for aluminum machining?
Answer: High spindle speeds are crucial for aluminum machining because they allow for faster material removal, which reduces cycle times and increases productivity. They also help achieve a smoother surface finish and can extend tool life by reducing cutting forces and heat generation.
3. Can a 3-axis machining center handle complex aluminum parts?
Answer: While a 3-axis machining center can handle some complex parts, it may not be the best option for highly intricate designs. A multi-axis machining center, such as a 5-axis machine, is better suited for complex parts as it can machine from multiple angles in a single setup, reducing the risk of alignment errors and improving accuracy.
4. What are the advantages of using a bridge mill for aluminum?
Answer: Bridge mills are particularly advantageous for machining large and heavy aluminum parts. They offer a large work envelope, robust structure, and stability, which are essential for maintaining accuracy and surface finish on large components. They are also highly customizable, allowing you to tailor the machine to your specific needs.
5. How does a horizontal machining center improve chip evacuation?
Answer: A horizontal machining center (HMC) improves chip evacuation by positioning the spindle horizontally. This orientation allows chips to fall away from the cutting area more easily, reducing the risk of tool damage and improving surface finish. HMCs often come with built-in chip conveyors and other features to further enhance chip management.
Conclusion
Choosing the right machining center for aluminum is crucial for achieving high-quality, efficient, and cost-effective results. High-speed machining centers, multi-axis machines, bridge mills, vertical machining centers, and horizontal machining centers each have their unique advantages and are best suited for different applications. By considering factors such as spindle speed, tooling, coolant system, rigidity, and automation capabilities, you can select the machine that best meets your needs and ensures the best outcomes for your aluminum machining projects.
I hope this article has provided you with valuable insights into the types of machining centers that are suitable for aluminum and the factors to consider when making your choice. If you have any further questions or need more detailed information, feel free to reach out!