When it comes to choosing materials for construction, manufacturing, and various industrial applications, the debate between steel and aluminum is a common one. Both materials have their unique properties and are widely used, but steel often stands out for its superior strength. In this article, I’ll delve into why steel is stronger than aluminum, exploring the scientific and practical aspects that make it a preferred choice in many scenarios.
The Basics: Understanding Steel and Aluminum
Before we dive into the specifics, let’s take a moment to understand what steel and aluminum are.
Steel: A Versatile Alloy
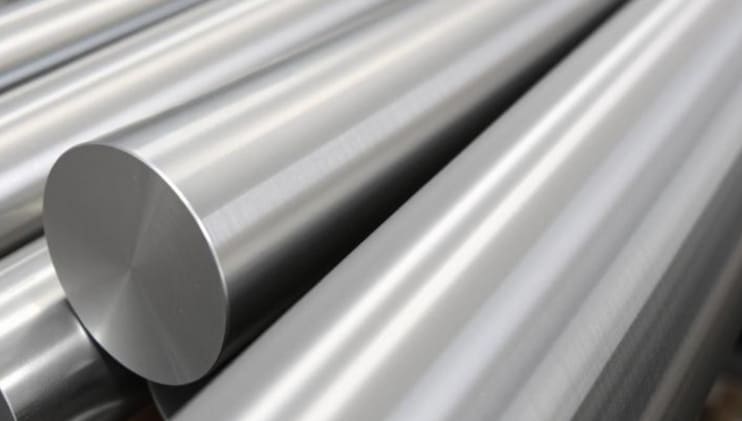
Steel is an alloy primarily composed of iron and carbon, with small amounts of other elements like manganese, silicon, and sometimes nickel and chromium. The carbon content in steel can vary, which significantly affects its properties. Generally, the higher the carbon content, the stronger and harder the steel, but it also becomes more brittle.
Aluminum: A Lightweight Metal
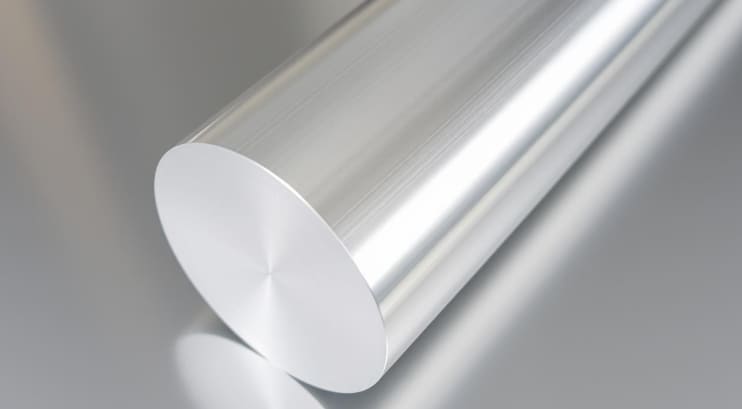
Aluminum, on the other hand, is a pure metal known for its lightweight and corrosion-resistant properties. It is often alloyed with other elements like copper, magnesium, and zinc to enhance its strength and durability. Despite its lower density, aluminum is widely used in applications where weight is a critical factor, such as in the aerospace and automotive industries.
The Science Behind Strength
Atomic Structure and Bonding
The strength of a material is largely determined by its atomic structure and the type of bonding between its atoms. Steel, being an alloy of iron and carbon, has a more complex atomic structure compared to pure aluminum. The iron atoms in steel are arranged in a body-centered cubic (BCC) structure, which is inherently strong. The addition of carbon atoms disrupts this structure, creating dislocations that make the material even stronger.
Aluminum, on the other hand, has a face-centered cubic (FCC) structure, which is more ductile and less prone to brittle fracture. While this structure allows aluminum to be more malleable and formable, it also means that it is less strong compared to steel.
Yield Strength and Tensile Strength
Yield strength and tensile strength are two key measures of a material’s strength. Yield strength is the point at which a material begins to deform permanently, while tensile strength is the maximum stress that a material can withstand before breaking.
Material | Yield Strength (MPa) | Tensile Strength (MPa) |
---|---|---|
Steel | 250 – 1,500 | 400 – 2,000 |
Aluminum | 70 – 500 | 90 – 600 |
As you can see from the table, steel has a significantly higher yield and tensile strength compared to aluminum. This means that steel can withstand more stress and force before it deforms or breaks.
Density and Weight
While strength is a crucial factor, weight is also an important consideration in many applications. Steel is much denser than aluminum, which means that a piece of steel will be heavier than an equivalent piece of aluminum. This can be a disadvantage in applications where weight is a critical factor, such as in aircraft or vehicles, where reducing weight can improve fuel efficiency and performance.
Corrosion Resistance
Both steel and aluminum have different levels of corrosion resistance. Stainless steel, a type of steel that contains chromium, is highly resistant to corrosion. However, ordinary steel can rust if not properly treated, which can weaken the material over time. Aluminum, on the other hand, naturally forms a protective oxide layer when exposed to air, which prevents further corrosion. This makes aluminum a better choice in environments where corrosion is a concern.
Practical Applications and Considerations
Construction and Infrastructure
In the construction industry, steel is the go-to material for structural components such as beams, columns, and reinforcement bars. Its high strength and durability make it ideal for supporting heavy loads and withstanding environmental stresses. Steel is also used in bridges, skyscrapers, and other large-scale structures where strength and stability are paramount.
Automotive Industry
In the automotive industry, the choice between steel and aluminum depends on the specific requirements of the vehicle. While steel is used for the chassis and structural components due to its strength, aluminum is often used for body panels and other parts to reduce weight and improve fuel efficiency. The combination of both materials allows manufacturers to optimize performance and safety.
Aerospace and Aviation
The aerospace industry is another sector where the choice of material is critical. Aluminum is widely used in aircraft due to its lightweight and corrosion-resistant properties. However, certain critical components, such as engine parts and landing gear, are made from steel or steel alloys to ensure maximum strength and durability.
Consumer Goods
In consumer goods, both steel and aluminum are used, but for different purposes. Steel is often used in appliances and tools where strength and durability are important, while aluminum is used in products like cookware and electronics where weight and corrosion resistance are key factors.
FAQs
What is the main difference between steel and aluminum?
The main difference between steel and aluminum is their composition and properties. Steel is an alloy of iron and carbon, known for its high strength and durability, while aluminum is a pure metal known for its lightweight and corrosion-resistant properties.
Which is better for construction: steel or aluminum?
Steel is generally better for construction due to its higher strength and ability to support heavy loads. However, aluminum can be used in certain applications where weight is a critical factor.
Can aluminum be as strong as steel?
While aluminum can be strengthened through alloying and heat treatment, it generally cannot match the strength of steel. However, aluminum alloys can achieve strength levels that are suitable for many applications, especially where weight is a concern.
Is steel more expensive than aluminum?
Steel is generally less expensive than aluminum, especially when considering the cost per unit of strength. However, the cost can vary depending on the specific grade and form of the material.
Which material is better for the environment?
Both steel and aluminum have environmental impacts, but they differ in terms of production and recycling. Steel production is more energy-intensive, but steel is highly recyclable and can be reused multiple times without losing its properties. Aluminum production is less energy-intensive, and aluminum is also highly recyclable, making it a more sustainable choice in many cases.
Conclusion
In conclusion, steel is stronger than aluminum due to its complex atomic structure, higher yield and tensile strength, and greater density. While aluminum has its own advantages, such as being lightweight and corrosion-resistant, steel remains the preferred choice for applications where strength and durability are paramount. Understanding the properties and applications of both materials can help you make informed decisions when choosing the right material for your project.
Whether you’re building a skyscraper, designing a car, or creating consumer goods, the choice between steel and aluminum will depend on the specific requirements of your application. By weighing the pros and cons of each material, you can ensure that your project is both strong and efficient.
I hope this article has provided you with a comprehensive understanding of why steel is stronger than aluminum and how each material can be used effectively in various industries. If you have any more questions or need further information, feel free to reach out!