In the world of modern manufacturing, two technologies stand out as game changers: CNC (Computer Numerical Control) Machining and 3D Printing. Both methods offer unique advantages and are used in a variety of industries, from automotive to aerospace. But which one is better? Let’s dive into the details to help you make an informed decision.
CNC Machining: Precision and Power
CNC (Computer Numerical Control) machining is a subtractive manufacturing process. Imagine starting with a solid block of material and then precisely carving away at it until your desired shape emerges. This is exactly what CNC machining does! Computer-controlled machines use a variety of cutting tools to remove material layer by layer, resulting in highly accurate and durable parts.
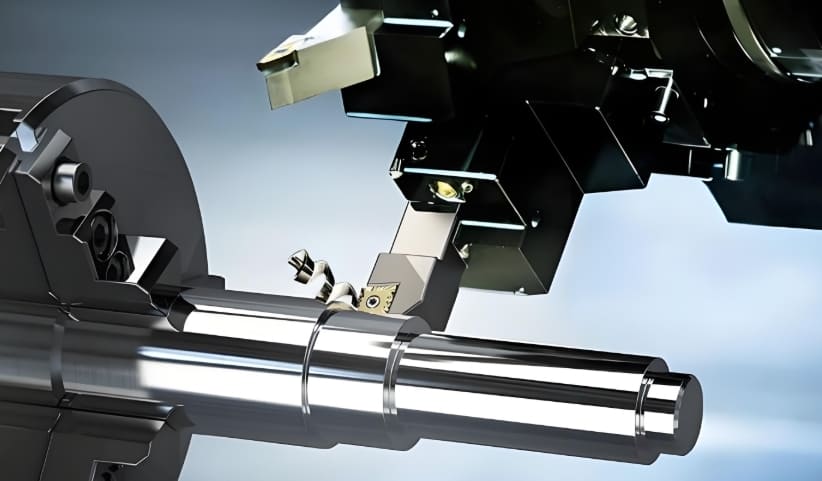
The Strengths of CNC Machining
- High Precision and Accuracy: CNC machining excels when tight tolerances and exact dimensions are crucial. It can consistently produce parts with exceptional accuracy.
- Excellent Material Selection: CNC machining works with a vast array of materials, including metals (aluminum, steel, titanium), plastics (ABS, polycarbonate, acrylic), and even wood.
- Superior Surface Finish: CNC-machined parts typically have a smooth and high-quality surface finish right off the machine, reducing or eliminating the need for extensive post-processing.
- High Volume Production: Once a CNC program is set up, producing large quantities of identical parts is relatively efficient and cost-effective.
- Strong Mechanical Properties: Parts created through CNC machining often exhibit excellent strength and durability due to the use of solid material.
Limitations of CNC Machining
- Geometric Constraints: Complex internal geometries or intricate designs can be challenging or impossible to create with CNC machining due to the limitations of cutting tool access.
- Material Waste: Because it’s a subtractive process, CNC machining generates more material waste compared to additive methods like 3D printing.
- Setup Costs: Setting up a CNC machine for a new part can involve significant upfront costs, including programming and tooling.
- Longer Lead Times for Prototypes: Creating a prototype using CNC machining might take longer compared to 3D printing, especially for complex designs.
3D Printing: Freedom and Flexibility
3D printing, also known as additive manufacturing, takes a different approach. Instead of removing material, it builds parts layer by layer from a digital design. This allows for the creation of intricate geometries and complex shapes that would be impossible or impractical to produce using traditional methods.
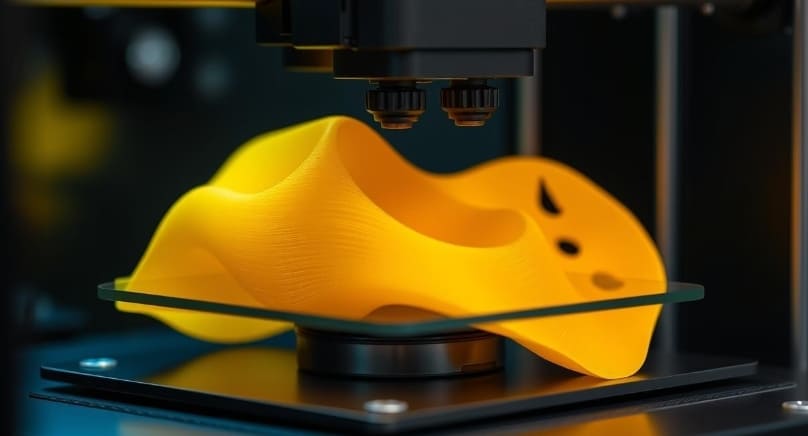
The Advantages of 3D Printing
- Design Freedom: 3D printing shines when it comes to complex geometries and intricate internal structures. It allows for designs that would be impossible or extremely difficult to manufacture using traditional methods.
- Rapid Prototyping: 3D printing is ideal for creating prototypes quickly and affordably. You can iterate on designs rapidly and test them before committing to a final product.
- Customization: 3D printing enables mass customization, allowing you to tailor products to individual needs and preferences without significant cost increases.
- Tooling Free: There is no need for specialized tooling like molds or dies.
- Reduced Material Waste: Because it builds parts layer by layer, 3D printing typically generates less material waste compared to CNC machining.
The Drawbacks of 3D Printing
- Material Limitations: While the range of 3D printable materials is expanding, it is still more limited than the materials available for CNC machining.
- Lower Mechanical Properties: 3D-printed parts may not always have the same strength and durability as CNC-machined parts, depending on the printing technology and materials used.
- Surface Finish: 3D-printed parts often require post-processing to achieve a smooth surface finish.
- Slower Production Speeds for High Volumes: 3D printing can be slower and more expensive for high-volume production compared to CNC machining.
- Accuracy and Tolerances: While improving, 3D printing may not always achieve the same level of precision and tight tolerances as CNC machining, especially for certain printing technologies.
Key Similarities Between 3D Printing and CNC Machining
While CNC machining and 3D printing are different processes, they share several similarities that make them both valuable tools in modern manufacturing:
- Digital Design: Both methods start with a digital design file, which is essential for creating the part.
- Automation: Both processes are highly automated, reducing the need for manual labor and increasing consistency.
- Material Range: Both can work with a variety of materials, although the specific types and properties may differ.
- Quality Control: Both methods allow for precise control over the final product, ensuring high-quality results.
Differences Between 3D Printing and CNC Machining
Despite their similarities, 3D printing and CNC milling have distinct differences that can impact the choice of manufacturing method:
- Process Type:
- CNC Machining: Subtractive process where material is removed from a solid block.
- 3D Printing: Additive process where material is added layer by layer to build the part.
- Material Efficiency:
- CNC Machining: Can result in significant material waste, especially for complex parts.
- 3D Printing: Uses only the necessary amount of material, reducing waste and potentially lowering costs.
- Production Scale:
- CNC Machining: More cost-effective for large production runs due to economies of scale.
- 3D Printing: More cost-effective for small production runs and prototyping due to lower setup costs.
- Lead Time:
- CNC Machining: May have longer lead times due to the need for tooling and setup.
- 3D Printing: Can have shorter lead times, especially for small, detailed parts.
- Post-Processing:
- CNC Machining: Often requires minimal post-processing, as the parts are already close to their final form.
- 3D Printing: May require additional post-processing steps, such as sanding, painting, or heat treating, to achieve the desired finish.
Comparing Subtractive and Additive Manufacturing
The fundamental difference between CNC machining and 3D printing lies in their manufacturing processes:
- Subtractive Manufacturing (CNC Machining):
- Process: Material is removed from a solid block to create the final part.
- Advantages: High precision, suitability for a wide range of materials, and ability to handle large production runs.
- Disadvantages: Can be expensive for small runs, may produce significant material waste, and requires tooling and setup.
- Additive Manufacturing (3D Printing):
- Process: Material is added layer by layer to build the final part.
- Advantages: Ability to create complex geometries, minimal material waste, and cost-effective for small production runs.
- Disadvantages: May require additional post-processing, can be slower for large parts, and may not achieve the same level of precision as CNC machining.
Key Decision Factors When Choosing a Manufacturing Type
When deciding between CNC machining and 3D printing, several factors should be considered:
- Production Volume:
- Large Runs: CNC machining is generally more cost-effective for large production volumes.
- Small Runs: 3D printing is more cost-effective for small production runs and prototyping.
- Material Requirements:
- Strong, Durable Materials: CNC machining is better suited for materials that require high strength and durability, such as metals.
- Complex, Lightweight Materials: 3D printing is ideal for materials that need to be lightweight or have complex internal structures, such as plastics and composites.
- Design Complexity:
- Simple Geometries: CNC machining can handle simple geometries efficiently.
- Complex Geometries: 3D printing excels at creating parts with intricate designs and internal structures.
- Lead Time:
- Short Lead Time: 3D printing can produce parts quickly, making it ideal for urgent projects.
- Long Lead Time: CNC machining may have longer lead times due to the need for setup and tooling.
- Cost:
- High Initial Cost: CNC machining has a higher initial setup cost but is more cost-effective for large production runs.
- Low Initial Cost: 3D printing has a lower initial setup cost but may become more expensive for large volumes.
Advantages of CNC Machining Compared to 3D Printing
While 3D printing has its advantages, CNC machining still holds several key benefits:
- Precision and Surface Finish:
- CNC machining can achieve extremely tight tolerances and smooth surface finishes, which are crucial for high-precision applications.
- Material Strength:
- CNC-machined parts are often stronger and more durable, especially when using metals and high-strength plastics.
- Large Parts:
- CNC machining is better suited for producing large parts, as 3D printers may have size limitations.
- Versatility:
- CNC machines can perform a wide range of operations, including drilling, milling, and turning, making them more versatile for different manufacturing needs.
- Economies of Scale:
- The cost per unit decreases significantly with larger production runs, making CNC machining more cost-effective for mass production.
Comparison Table: CNC Machining vs. 3D Printing
Feature | CNC Machining | 3D Printing |
---|---|---|
Process Type | Subtractive | Additive |
Material Efficiency | Can produce significant waste | Minimal waste, material-saving |
Production Scale | More cost-effective for large runs | Cost-effective for small runs and prototyping |
Lead Time | Longer due to setup and tooling | Shorter for small, detailed parts |
Post-Processing | Often minimal | May require additional steps |
Precision | Extremely tight tolerances | Moderate to high (depends on technology) |
Material Strength | Strong and durable (especially metals) | Can be less strong, depends on material |
Design Complexity | Suitable for simple geometries | Ideal for complex geometries and internal structures |
Initial Cost | Higher (tooling and setup) | Lower (no tooling required) |
Part Size | Can handle large parts | May have size limitations |
FAQs
Q: What is the main difference between CNC machining and 3D printing?
A: The main difference is the manufacturing process. CNC machining is a subtractive process where material is removed from a solid block, while 3D printing is an additive process where material is added layer by layer.
Q: Is CNC machining more accurate than 3D printing?
A: Generally, CNC machining can achieve tighter tolerances and higher precision, especially for metal parts. However, some advanced 3D printing technologies can also produce highly accurate parts.
Q: Can 3D printing replace CNC machining?
A: While 3D printing is a powerful tool, it cannot fully replace CNC machining. Each method has its strengths and is better suited for different applications. For example, 3D printing is excellent for prototyping and small production runs, while CNC machining is better for large-scale production and parts requiring high strength and durability.
Q: Which method is more cost-effective for small production runs?
A: 3D printing is typically more cost-effective for small production runs and prototyping due to its lower setup costs and ability to customize each part without additional tooling.
Q: What are the common materials used in CNC machining and 3D printing?
- CNC Machining: Metals (steel, aluminum, titanium), plastics, composites, and wood.
- 3D Printing: Plastics (PLA, ABS, PETG), resins, metals (stainless steel, aluminum), and bio-inks.
Conclusion
Choosing between CNC machining and 3D printing depends on your specific project requirements. CNC machining is ideal for high-precision, large production runs, and parts made from strong, durable materials. On the other hand, 3D printing is perfect for small production runs, prototyping, and parts with complex geometries. By understanding the strengths and limitations of each method, you can make the best decision for your manufacturing needs.
Whether you’re a seasoned engineer or a DIY enthusiast, both CNC machining and 3D printing offer exciting opportunities to bring your designs to life. So, the next time you’re faced with a manufacturing decision, consider the unique benefits of each technology and choose the one that best fits your project.