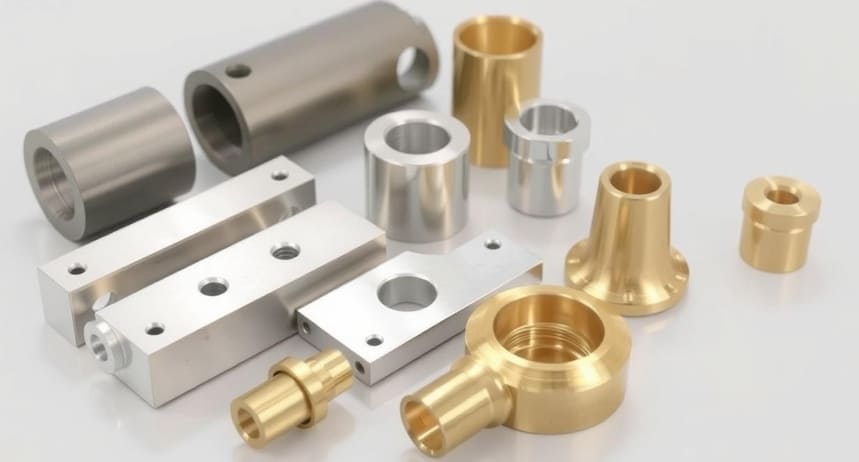
As a professional in the CNC machining industry, I’ve had the privilege of working with a variety of materials, each with its unique properties and challenges. Two of the most commonly used materials are brass and aluminum. Both are highly versatile and find applications in numerous industries, from aerospace to jewelry making. However, when it comes to CNC machining, one might wonder which is easier to work with. In this article, I’ll delve into the properties of brass and aluminum, compare them in terms of machining, and provide some recommended practices for working with each material. Let’s get started!
Properties of Brass
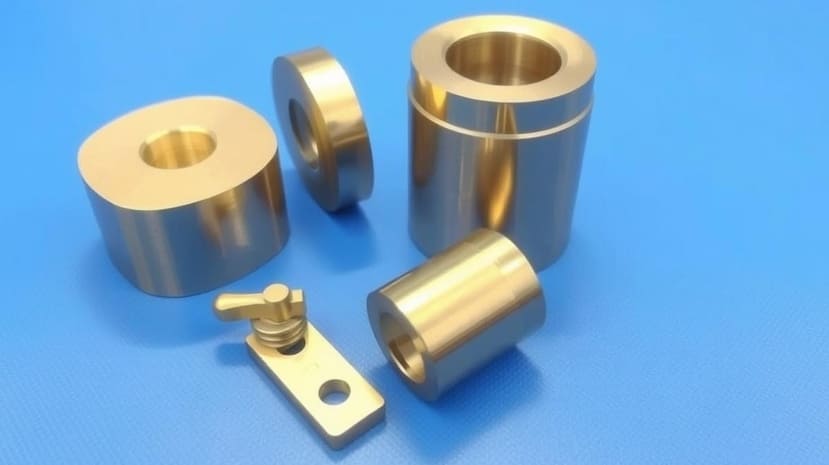
- Composition: Brass is an alloy primarily composed of copper and zinc. The exact composition can vary, which affects its properties.
- Strength: Brass is relatively strong and durable, making it suitable for applications that require resistance to corrosion and wear.
- Conductivity: Brass has good thermal and electrical conductivity, which can be beneficial in certain applications.
- Appearance: Brass has a naturally attractive golden color that can be polished to a high shine.
- Workability: Brass is generally easy to machine, but it can be more challenging than aluminum due to its higher hardness and tendency to work-harden.
Properties of Aluminum
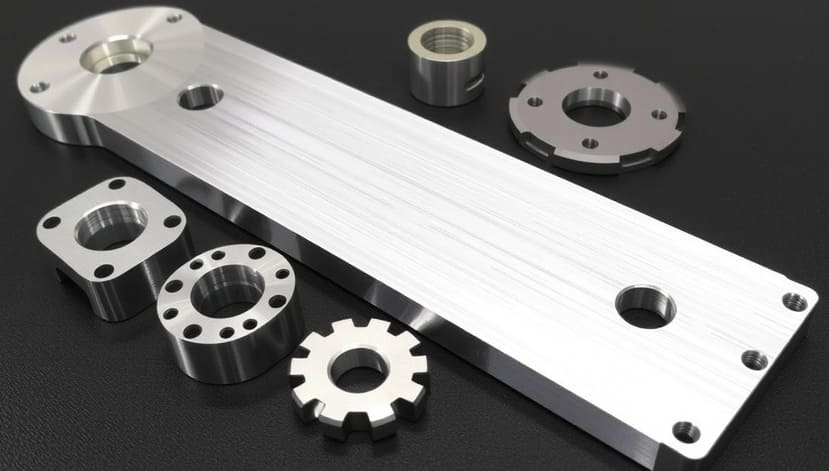
- Composition: Aluminum is a pure metal, but it is often alloyed with other elements like silicon, magnesium, and copper to enhance its properties.
- Strength: Aluminum is lightweight but relatively strong, making it ideal for applications where weight reduction is crucial.
- Conductivity: Aluminum has excellent thermal and electrical conductivity, which is why it’s often used in heat sinks and electrical components.
- Appearance: Aluminum has a silvery appearance that can be anodized to various colors and finishes.
- Workability: Aluminum is generally easier to machine than brass due to its lower hardness and better machinability.
Best Brass Grades for CNC Machining
Brass is a popular choice for CNC machining due to its excellent machinability, aesthetics, and corrosion resistance. However, not all brass grades are created equal. Here are some of the best brass grades for CNC machining and their properties:
1. C36000 (Free-Cutting Brass)
- Properties: High machinability, good strength, and excellent surface finish.
- Applications: Ideal for intricate parts, fittings, and components that require a high level of detail and precision.
- Why Choose It: The addition of lead makes it easier to cut, reducing tool wear and improving machining efficiency.
2. C26000 (Cartridge Brass)
- Properties: Good machinability, high ductility, and excellent formability.
- Applications: Commonly used in ammunition casings, musical instruments, and decorative items.
- Why Choose It: Its balanced properties make it versatile for a wide range of applications.
3. C46400 (Naval Brass)
- Properties: Excellent corrosion resistance, good strength, and machinability.
- Applications: Suitable for marine hardware, plumbing fixtures, and architectural components.
- Why Choose It: Its high resistance to saltwater corrosion makes it ideal for outdoor and marine environments.
Best Aluminum Grades for CNC Machining
Aluminum is another widely used material in CNC machining, known for its lightweight, high strength-to-weight ratio, and excellent thermal conductivity. Here are the top aluminum grades for CNC machining:
1. 6061 T6
- Properties: Good machinability, high strength, and excellent corrosion resistance.
- Applications: Aerospace, automotive, and structural components.
- Why Choose It: It provides a good balance of strength and machinability, making it a versatile choice.
2. 7075 T6
- Properties: Exceptional strength, high hardness, and good machinability.
- Applications: Aircraft parts, military equipment, and high-stress components.
- Why Choose It: It’s one of the strongest aluminum alloys, suitable for demanding applications.
3. 2024 T3
- Properties: High strength, good fatigue resistance, and fair machinability.
- Applications: Airframe structures, fasteners, and structural components.
- Why Choose It: Known for its high strength and good fatigue resistance, it’s a popular choice in the aerospace industry.
Machinability: A Key Factor
Machinability refers to how easily a material can be cut, shaped, or finished during machining processes. Several factors contribute to a material’s machinability, including its hardness, ductility, thermal conductivity, and the type of chips it produces.
Brass: The Machining Favorite
In my experience, brass generally earns the title of “easier to machine” for several reasons:
- Self-Lubricating Properties: Brass has a natural lubricity due to its copper content, reducing friction between the cutting tool and the workpiece. This leads to smoother cuts, less tool wear, and better surface finishes.
- Brittle Chips: Brass produces short, brittle chips that break easily. This is a significant advantage because these chips are less likely to get tangled around the cutting tool or the workpiece, which can cause scratches or other imperfections.
- Lower Cutting Forces: Brass typically requires lower cutting forces compared to aluminum. This means less stress on your machine and tools, making it easier to achieve precise cuts.
Aluminum: The Lightweight Contender
While brass has its advantages, aluminum also has its own set of characteristics that can make it a suitable choice for machining:
- High Speed Machining: Aluminum can be machined at very high speeds, which leads to faster production times. This is particularly useful for large-scale projects where time is of the essence.
- Lightweight: Aluminum’s low density makes it ideal for applications where weight is a concern. Machining aluminum components can significantly reduce the overall weight of a product.
- Good Thermal Conductivity: Aluminum’s excellent thermal conductivity helps dissipate heat quickly during machining. This reduces the risk of the workpiece overheating, which can lead to dimensional inaccuracies and poor surface finishes.
Comparison of Brass and Aluminum in CNC Machining
When it comes to CNC machining, several factors can influence the ease and efficiency of working with a material. Let’s break down the key considerations:
Cost Considerations:
-
- Brass: Brass tends to be more expensive than aluminum. The cost can vary depending on the specific alloy and market conditions.
- Aluminum: Aluminum is generally more cost-effective, especially for large-scale production. It’s also widely available, which can reduce lead times and costs.
- Conclusion: If budget is a primary concern, aluminum is often the better choice.
Machining Complexity and Precision:
-
- Brass: Brass can be more challenging to machine due to its higher hardness and tendency to work-harden. However, it is still relatively easy to achieve high precision with the right tools and techniques.
- Aluminum: Aluminum is softer and more malleable, making it easier to machine and achieve precise tolerances. It’s also less likely to work-harden, which reduces the risk of tool breakage.
- Conclusion: Aluminum is generally easier to machine for high-precision applications.
Tool Wear and Tool Life:
-
- Brass: Machining brass can cause more wear on cutting tools due to its higher hardness and the tendency to generate heat. This can result in shorter tool life and increased maintenance costs.
- Aluminum: Aluminum is less abrasive and generates less heat during machining, which can extend tool life and reduce maintenance costs.
- Conclusion: Aluminum is more tool-friendly, leading to longer tool life and lower costs.
Surface Finish and Aesthetics:
-
- Brass: Brass can achieve a very smooth and polished surface finish, which is highly desirable for decorative and functional parts. However, it requires careful handling and precision to avoid scratches and tool marks.
- Aluminum: Aluminum can also achieve a high-quality surface finish, but it may require additional processes like anodizing or painting to enhance its aesthetics.
- Conclusion: Both materials can produce excellent surface finishes, but brass may require more attention to detail.
Specific Applications:
-
- Brass: Brass is often used in applications where appearance and corrosion resistance are important, such as musical instruments, decorative hardware, and plumbing fixtures.
- Aluminum: Aluminum is widely used in aerospace, automotive, and electronics industries due to its lightweight, strength, and conductivity. It’s also popular for structural components and heat sinks.
- Conclusion: The choice between brass and aluminum often depends on the specific requirements of the project.
Recommended Practices for CNC Machining Brass and Aluminum
Knowing the best practices for machining each material can significantly improve the efficiency and quality of your work. Here are some tips for working with brass and aluminum:
Brass Machining:
- Tool Selection: Use carbide tools for brass machining to handle the higher hardness and reduce tool wear. High-speed steel (HSS) tools can also be used for smaller, less demanding jobs.
- Coolant: Apply a cutting fluid or coolant to reduce heat and extend tool life. Brass can generate significant heat, which can cause the material to expand and affect precision.
- Speeds and Feeds: Use lower cutting speeds and feeds compared to aluminum to avoid work-hardening and tool damage.
- Finishing: Brass can be polished to a high shine, but it’s crucial to use fine-grit abrasives and a consistent technique to achieve a uniform finish.
Aluminum Machining:
- Tool Selection: Aluminum is well-suited for both carbide and HSS tools. Carbide tools are generally preferred for high-speed machining and longer tool life.
- Coolant: While aluminum doesn’t generate as much heat as brass, using a coolant can still help reduce friction and improve surface finish.
- Speeds and Feeds: Aluminum can be machined at higher speeds and feeds, which can increase productivity. However, be cautious not to overheat the material, as it can lead to tool wear and poor surface finish.
- Finishing: Aluminum can be anodized, painted, or chemically treated to enhance its appearance and protect it from corrosion. Anodizing is a popular choice for creating a durable, colored finish.
Both Materials:
- Machine Maintenance: Regularly inspect and maintain your CNC machine to ensure it’s in optimal condition. This includes cleaning the machine, checking for wear, and lubricating moving parts.
- Workholding: Use high-quality workholding devices to secure the material firmly. This can help prevent vibration and ensure precise cuts.
- Programming: Invest in high-quality CNC programming to optimize the machining process. Efficient toolpaths and accurate G-code can help reduce machining time and improve quality.
- Safety: Always follow safety protocols when machining. Wear appropriate personal protective equipment (PPE) and ensure the machine is properly guarded.
Table: Comparison of Brass and Aluminum in CNC Machining
Factor | Brass | Aluminum |
---|---|---|
Cost | More expensive, varies by alloy | Less expensive, widely available |
Hardness | Higher, can work-harden | Lower, more malleable |
Thermal Conductivity | Good, but can generate heat | Excellent, less heat generation |
Electrical Conductivity | Good, useful in electrical components | Excellent, widely used in electronics and heat sinks |
Surface Finish | Can achieve a high polish, requires careful handling | Can achieve a high-quality finish, may need additional treatments |
Tool Wear | Higher, shorter tool life | Lower, longer tool life |
Specific Applications | Decorative hardware, plumbing, musical instruments | Aerospace, automotive, electronics, structural components |
Machining Speed | Lower speeds and feeds to avoid work-hardening | Higher speeds and feeds for efficiency |
Coolant Use | Essential to reduce heat and improve tool life | Recommended to reduce friction and improve surface finish |
FAQs
Q: Which material is better for high-precision CNC machining?
- A: Aluminum is generally better for high-precision CNC machining due to its lower hardness and better machinability. However, brass can also achieve high precision with the right techniques and tools.
Q: Can brass and aluminum be anodized?
- A: Aluminum can be anodized to improve corrosion resistance and appearance. Brass, on the other hand, is typically polished or plated rather than anodized.
Q: How does the choice of material affect the overall cost of a CNC project?
- A: Brass is generally more expensive than aluminum, which can increase the overall cost of a CNC project. However, the cost difference can be offset by the material’s properties and the specific requirements of the application.
Q: Are there any environmental considerations when choosing between brass and aluminum?
- A: Both materials are recyclable, but aluminum is more widely recycled due to its lower cost and higher demand. Brass can also be recycled, but the process may be more complex due to its alloy composition.
Q: What are some common issues to watch out for when machining brass?
- A: Common issues include work-hardening, tool wear, and heat generation. Careful selection of tools and cutting parameters can help mitigate these issues.
Q: Can I use the same cutting tools for both brass and aluminum?
- A: While some cutting tools can be used for both materials, it’s generally better to use specialized tools for each. Brass requires harder tools like carbide, while aluminum can be machined with both carbide and HSS tools.
Conclusion
In the world of CNC machining, both brass and aluminum have their strengths and weaknesses. Brass is more expensive and can be more challenging to machine, but it offers excellent corrosion resistance and a beautiful finish. Aluminum, on the other hand, is cost-effective, easy to machine, and highly versatile. The choice between the two often depends on the specific requirements of the project, such as budget, precision, and application.
By following the recommended practices and understanding the properties of each material, you can ensure that your CNC machining projects are both efficient and of high quality. Whether you choose brass for its aesthetic appeal or aluminum for its practicality, the right approach will help you achieve the best results.
I hope this article has been helpful in comparing brass and aluminum in CNC machining. If you have any questions or need further guidance, feel free to reach out!