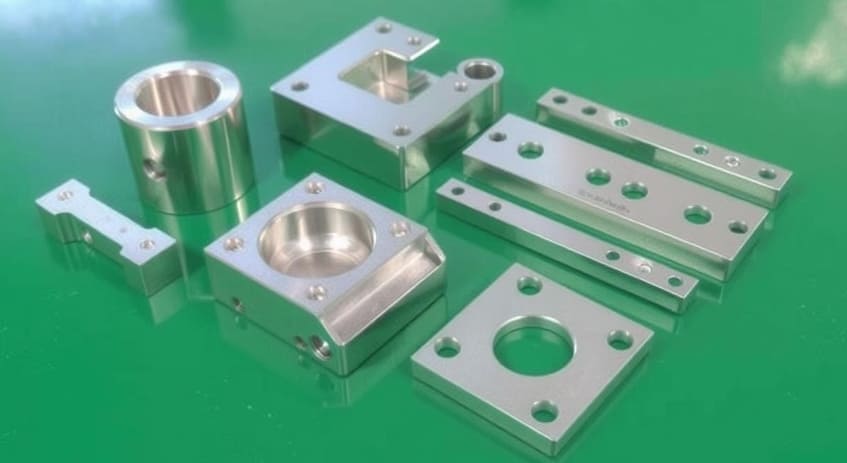
Aluminium is one of the most versatile and widely used metals in the world. Known for its lightweight, corrosion-resistant properties, and excellent formability, aluminum is a favorite in various industries, from aerospace to construction. However, not all aluminum is created equal. Some aluminum alloys are stronger and more durable than others, making them ideal for applications that require high strength and performance. In this article, I’ll delve into the world of the strongest aluminum alloys, exploring their properties, applications, and why they stand out.
Understanding Aluminum Alloys
Before we dive into the specifics of the strongest aluminum alloys, it’s essential to understand what aluminum alloys are and how they differ from pure aluminum. Aluminum alloys are mixtures of aluminum and other elements, such as copper, magnesium, silicon, and zinc. These elements are added to enhance the properties of pure aluminum, such as strength, corrosion resistance, and formability.
Types of Aluminum Alloys
Aluminum alloys are typically classified into two main categories: wrought and cast. Wrought alloys are those that can be shaped through mechanical processes like rolling, extruding, or forging. Cast alloys, on the other hand, are poured into molds and solidified. Each category has its own set of subcategories, which are further divided based on the primary alloying elements and their properties.
Factors Affecting the Strength of Aluminum Alloys
Before we get into specific alloy designations, it’s important to realize that several factors influence the final strength of an aluminum alloy:
- Alloying Elements: The type and percentage of alloying elements have the most significant impact.
- Heat Treatment: Processes like solution heat treating, quenching, and artificial aging can dramatically increase strength.
- Manufacturing Process: How the alloy is processed (e.g., casting, forging, extrusion) affects its grain structure and overall properties.
- Work Hardening: Cold working the metal increases the number of dislocations, making it more resistant to deformation.
The Strongest Aluminum Alloys
When it comes to strength, certain aluminum alloys stand out. These alloys are often used in high-performance applications where weight, strength, and durability are critical. Here are some of the strongest aluminum alloys and their key characteristics:
7075 Aluminum
Properties:
- Yield Strength: 503 MPa (72,500 psi)
- Tensile Strength: 572 MPa (82,900 psi)
- Elongation: 10-15%
Applications:
- Aerospace: Used in aircraft structures, wings, and fuselages.
- Sports Equipment: Common in high-performance bicycles, golf clubs, and archery bows.
- Military: Used in body armor and vehicle components.
Why It’s Strong: 7075 aluminum is one of the strongest aluminum alloys available. It contains significant amounts of zinc, magnesium, and copper, which contribute to its exceptional strength and hardness. However, it is less formable than some other alloys, making it more challenging to work with in certain applications.
2024 Aluminum
Properties:
- Yield Strength: 324 MPa (47,000 psi)
- Tensile Strength: 448 MPa (65,000 psi)
- Elongation: 12-18%
Applications:
- Aerospace: Used in aircraft wings, fuselages, and structural components.
- Automotive: Used in high-performance car parts and racing components.
- Marine: Used in boat hulls and other marine structures.
Why It’s Strong: 2024 aluminum is known for its excellent strength-to-weight ratio and good fatigue resistance. It contains copper, which enhances its strength and corrosion resistance. However, it is more susceptible to stress corrosion cracking compared to some other alloys.
6061 Aluminum
Properties:
- Yield Strength: 241 MPa (35,000 psi)
- Tensile Strength: 310 MPa (45,000 psi)
- Elongation: 12-18%
Applications:
- Construction: Used in building frames, window and door frames, and structural supports.
- Bicycles: Common in bicycle frames and components.
- Marine: Used in boat parts and marine hardware.
Why It’s Strong: 6061 aluminum is a versatile and widely used alloy. It offers a good balance of strength, formability, and corrosion resistance. It is easier to weld and machine compared to some other high-strength alloys, making it a popular choice for a wide range of applications.
7050 Aluminum
Properties:
- Yield Strength: 490 MPa (71,000 psi)
- Tensile Strength: 538 MPa (78,000 psi)
- Elongation: 10-15%
Applications:
- Aerospace: Used in aircraft structures and components.
- Automotive: Used in high-performance vehicle parts.
- Industrial: Used in heavy machinery and equipment.
Why It’s Strong: 7050 aluminum is another high-strength alloy that is particularly resistant to stress corrosion cracking. It contains zinc and magnesium, which contribute to its strength and durability. It is often used in applications where both strength and corrosion resistance are critical.
Comparison of the Strongest Aluminum Alloys
To better understand the differences between these strong aluminum alloys, let’s compare their key properties in a table:
Alloy | Yield Strength (MPa) | Tensile Strength (MPa) | Elongation (%) | Primary Applications |
---|---|---|---|---|
7075 | 503 | 572 | 10-15 | Aerospace, Sports Equipment, Military |
2024 | 324 | 448 | 12-18 | Aerospace, Automotive, Marine |
6061 | 241 | 310 | 12-18 | Construction, Bicycles, Marine |
7050 | 490 | 538 | 10-15 | Aerospace, Automotive, Industrial |
Factors to Consider When Choosing the Strongest Aluminum Alloys
When selecting the strongest aluminum alloy for a specific application, several factors should be considered:
- Strength Requirements: The primary factor is the strength needed for the application. For high-strength applications, alloys like 7075 and 7050 are often the best choices.
- Corrosion Resistance: If the application involves exposure to corrosive environments, alloys with good corrosion resistance, such as 6061 and 7050, should be considered.
- Formability: Some high-strength alloys, like 7075, are less formable than others. If the application requires complex shapes or extensive forming, more formable alloys like 6061 may be better.
- Cost: High-strength alloys can be more expensive. The cost should be balanced against the performance requirements of the application.
- Weldability: Some alloys, like 6061, are easier to weld than others. If welding is required, this should be taken into account.
FAQs About the Strongest Aluminum Alloys
What is the strongest aluminum alloy?
The strongest aluminum alloy is 7075, which has a yield strength of 503 MPa and a tensile strength of 572 MPa. It is widely used in aerospace and high-performance applications.
What is the difference between 7075 and 2024 aluminum?
7075 aluminum is stronger and harder than 2024 aluminum, but it is less formable. 2024 aluminum has better fatigue resistance and is more commonly used in aircraft structures.
Can 7075 aluminum be welded?
7075 aluminum can be welded, but it is more challenging to weld than some other alloys. Special techniques and equipment are often required to achieve a strong, high-quality weld.
What are the main applications of 6061 aluminum?
6061 aluminum is widely used in construction, bicycles, and marine applications. It offers a good balance of strength, formability, and corrosion resistance.
Is 7050 aluminum better than 7075?
7050 aluminum is slightly less strong than 7075 but offers better resistance to stress corrosion cracking. It is often used in applications where both strength and corrosion resistance are critical.
Conclusion
The world of aluminum alloys is vast and diverse, with each alloy offering unique properties and advantages. The strongest aluminum alloys, such as 7075, 2024, 6061, and 7050, are essential in high-performance applications where strength, durability, and reliability are paramount. By understanding the properties and applications of these alloys, you can make informed decisions when selecting the right material for your project. Whether you’re building an aircraft, a bicycle, or a marine vessel, the right aluminum alloy can make all the difference.