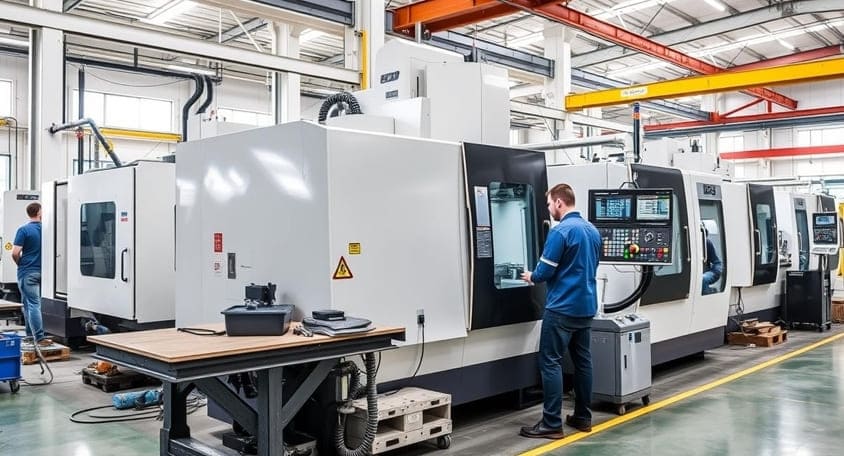
CNC machining is a versatile and precise manufacturing process that has revolutionized the way metal parts are produced. From aerospace components to intricate jewelry, CNC (Computer Numerical Control) machines can handle a wide range of materials and designs with incredible accuracy and efficiency. However, the cost of CNC machining can vary significantly, and understanding the factors that influence these costs is crucial for anyone looking to produce metal parts. In this article, I’ll break down the factors that influence CNC machining costs, additional cost considerations, and provide some tips on how to reduce these costs. Let’s dive in!
Factors Influencing the Cost of CNC Machining Metal Parts
When it comes to CNC machining, several key factors can influence the cost of producing metal parts. Here’s a detailed look at each:
- Material Costs
- Type of Metal: Different metals have different price points. For example, aluminum is generally less expensive than titanium.
- Grade of Metal: Within the same type of metal, the grade can also affect the cost. Higher-grade metals are typically more expensive.
- Availability: Rare or custom-ordered materials can be more costly due to their limited availability.
- Machining Time
- Complexity of the Part: More complex parts require more time to machine, which increases the cost.
- Number of Operations: Multiple operations, such as drilling, milling, and turning, can extend the machining time.
- Machine Speed: Different machines have varying speeds, which can impact the overall time and cost.
- Setup Costs
- Programming: The initial programming of the CNC machine can be a significant cost, especially for custom or complex parts.
- Tooling: Specialized tools may be required for certain designs, adding to the setup cost.
- Fixturing: The cost of creating or using existing fixtures can also affect the initial setup.
- Post-Machining Processes
- Finishing: Processes like polishing, sandblasting, and anodizing can add to the cost.
- Heat Treatment: Some metals require heat treatment to achieve specific properties, which can be an additional expense.
- Inspection: Thorough inspection to ensure quality can also add to the cost, especially for high-precision parts.
- Quantity
- Economies of Scale: Larger production runs can often reduce the cost per unit due to the amortization of setup costs over more parts.
- Batch Size: Small batches may incur higher setup costs, making them more expensive per unit.
- Machine and Labor Costs
- Machine Type: Different CNC machines have different operating costs. For instance, a 5-axis machine is more expensive to operate than a 3-axis machine.
- Labor Rates: The cost of labor can vary based on the location and expertise of the machinists.
- Design and Engineering
- Tolerances: Tighter tolerances require more precise machining and can be more expensive.
- Undercuts and Complex Features: Parts with undercuts or complex features can be more challenging to machine, increasing the cost.
Additional Cost Considerations in CNC Machining
Beyond the primary factors, there are several additional considerations that can influence the cost of CNC machining metal parts:
- Shipping and Handling
- Distance: The farther the parts need to be shipped, the higher the cost.
- Packing: Special packaging requirements, especially for fragile or high-precision parts, can add to the cost.
- Overhead Costs
- Facility Costs: Rent, utilities, and maintenance of the manufacturing facility contribute to the overall cost.
- Administrative Costs: Office staff, software, and other administrative expenses are part of the overhead.
- Quality Control
- Inspection Equipment: Advanced inspection equipment can be expensive but is necessary for ensuring high-quality parts.
- Certifications: Obtaining and maintaining certifications for quality and compliance can add to the cost.
- Material Waste
- Scrap Rates: The amount of material wasted during machining can affect the overall cost. Design optimization can help reduce this.
- Recycling: Some suppliers offer recycling services, which can offset the cost of material waste.
Strategies for Reducing CNC Machining Costs
Reducing the cost of CNC machining while maintaining quality is a common goal for many manufacturers. Here are some practical tips to help you achieve this:
- Optimize Your Design
- Simplify Geometry: Avoid unnecessary complex features that increase machining time.
- Use Standard Sizes: Design parts using standard material sizes to minimize waste.
- Reduce Tolerances: Only specify tight tolerances where absolutely necessary.
- Choose the Right Material
- Evaluate Alternatives: Consider using less expensive materials that meet your requirements.
- Bulk Buying: Purchasing materials in bulk can often reduce the cost per unit.
- Minimize Setup Costs
- Standardized Design: Use standardized designs whenever possible to reduce programming and tooling costs.
- Batch Production: Group similar parts together to minimize setup time.
- Leverage Economies of Scale
- Large Production Runs: Larger quantities can often reduce the cost per unit.
- Repeat Orders: Building a relationship with your supplier and placing repeat orders can lead to cost savings.
- Negotiate with Suppliers
- Long-Term Contracts: Consider signing long-term contracts with suppliers to secure better rates.
- Volume Discounts: Negotiate volume discounts for larger orders.
- Post-Machining Process Optimization
- Combine Operations: If possible, combine finishing operations to save time and money.
- Outsource Non-Critical Processes: Outsource less critical processes to reduce costs.
- Regular Maintenance
- Machine Maintenance: Regular maintenance can prevent costly breakdowns and downtime.
- Tool Maintenance: Keeping tools in good condition can improve efficiency and reduce the need for frequent replacements.
Cost Comparison Table
To give you a better idea of how these factors can impact the cost, here’s a simplified cost comparison table:
Factor | Low Cost Example | High Cost Example | Impact on Cost |
---|---|---|---|
Material | Aluminum 6061 | Titanium Grade 5 | Higher |
Machining Time | Simple flat part | Complex 3D part | Higher |
Setup Costs | Standard design | Custom, complex design | Higher |
Post-Machining | Minimal finishing (e.g., deburring) | Anodizing, heat treatment, polishing | Higher |
Quantity | 100 parts | 10 parts | Higher per unit |
Machine and Labor | 3-axis CNC machine, low labor rate | 5-axis CNC machine, high labor rate | Higher |
Design and Engineering | Loose tolerances, simple features | Tight tolerances, undercuts | Higher |
FAQs
Q: What is the most cost-effective metal for CNC machining?
A: Aluminum is often the most cost-effective metal for CNC machining due to its low density, good machinability, and relatively low cost compared to other metals like titanium or stainless steel.
Q: Can I reduce costs by choosing a less precise tolerance?
A: Yes, reducing the precision of your tolerances can lower costs. However, make sure that the less precise tolerances still meet your functional requirements.
Q: How much can I save by ordering in larger quantities?
A: The cost savings can vary, but generally, ordering in larger quantities can reduce the cost per unit by up to 30% or more, depending on the setup costs and the supplier’s pricing structure.
Q: Is it more cost-effective to have multiple parts machined at once?
A: Yes, machining multiple parts at once can reduce setup costs and improve efficiency, leading to cost savings.
Q: How can I estimate the cost of CNC machining?
A: Many suppliers offer online quoting tools that can help you estimate the cost based on your design and material choices. Additionally, you can request a detailed cost breakdown from your supplier to understand where the costs are coming from.
Q: What are some hidden costs in CNC machining?
A: Hidden costs can include material waste, additional finishing processes, and quality control inspections. It’s important to discuss these with your supplier to get a comprehensive cost estimate.
Conclusion
CNC machining is a powerful tool for producing high-quality metal parts, but the costs can vary widely depending on several factors. By understanding these factors and optimizing your design, material selection, and production process, you can significantly reduce the cost of CNC machining. Whether you’re a small business or a large corporation, taking the time to evaluate and negotiate with suppliers can help you get the best value for your money.
I hope this article provides a comprehensive and friendly overview of the costs involved in CNC machining metal parts. If you have any specific questions or need further details, don’t hesitate to ask!