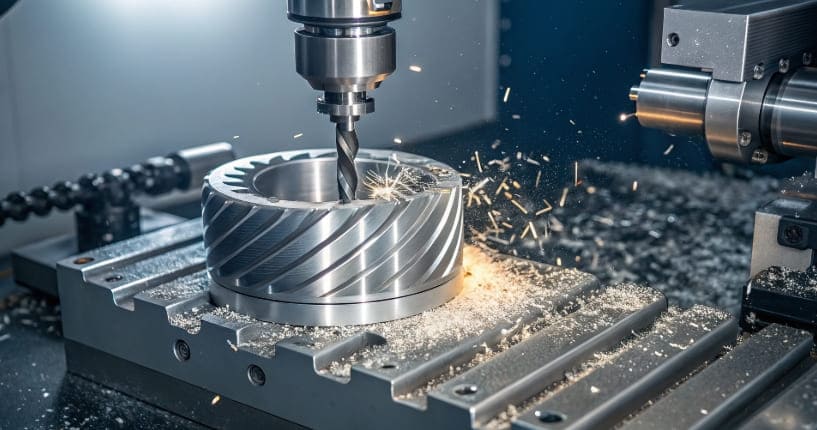
As a professional in the manufacturing industry, I have had the privilege of working with a wide range of materials and processes. However, one material and process combination that consistently stands out is aluminum CNC machining. This technology has revolutionized the way we create precision parts, and its benefits are numerous and significant. In this article, I will delve into the advantages of using aluminum in CNC machining, including its material properties, cost-effectiveness, and versatility. I’ll also provide some frequently asked questions (FAQs) and useful tips to help you understand and leverage this process in your projects.
Why Choose Aluminum for CNC Machining?
Aluminum is a popular choice for CNC machining for several reasons, primarily due to its unique properties and the precision that can be achieved. Let’s start by exploring why aluminum is such a go-to material in the manufacturing world.
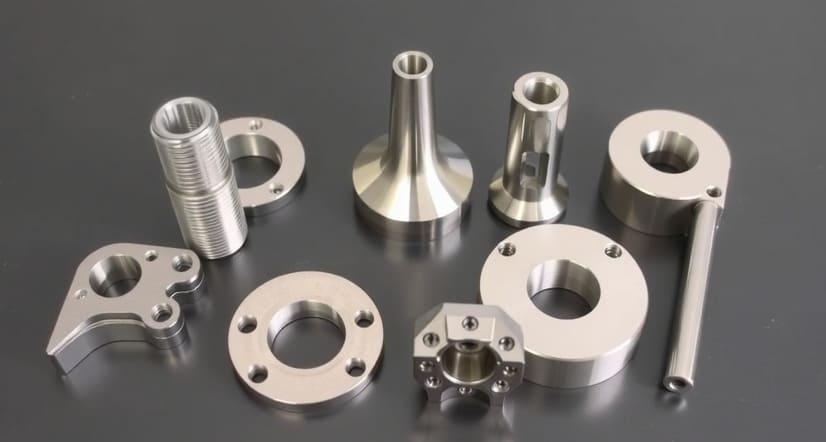
1. Lightweight and Strong
One of the most significant advantages of aluminum is its high strength-to-weight ratio. Aluminum is about one-third the weight of steel, making it an ideal material for applications where weight is a critical factor. For instance, in the aerospace and automotive industries, using aluminum can lead to significant fuel savings and improved performance.
2. Corrosion Resistance
Aluminum naturally forms a thin, protective oxide layer when exposed to air, which makes it highly resistant to corrosion. This property is particularly valuable in environments where parts are exposed to moisture, chemicals, or other corrosive agents. As a result, aluminum components have a longer lifespan and require less maintenance.
3. Thermal Conductivity
Aluminum has excellent thermal conductivity, which means it can efficiently transfer heat. This property is crucial in applications such as heat sinks, engine components, and cooling systems. By using aluminum, you can ensure that your products remain cool and perform optimally under high-temperature conditions.
4. Electrical Conductivity
In addition to its thermal properties, aluminum is also a good conductor of electricity. This makes it an ideal material for electrical components, such as circuit boards, connectors, and wiring systems. Its conductivity, combined with its lightweight nature, makes aluminum a top choice for many electrical applications.
5. Recyclability
Aluminum is 100% recyclable without any loss in quality. This not only makes it an environmentally friendly choice but also reduces material costs over the long term. Recycled aluminum can be used repeatedly, and its production requires significantly less energy compared to primary aluminum.
The Treasure Trove: Unveiling the Benefits of Aluminum CNC Machining
Now, let’s get to the heart of the matter: the benefits of using aluminum CNC machining. Here’s a detailed look at what makes this process so advantageous:
1. Precision and Accuracy: Hitting the Mark Every Time
CNC machining is renowned for its precision, and when combined with aluminum, the results are truly remarkable. The computer-controlled process ensures that parts are manufactured to extremely tight tolerances, often within a few thousandths of an inch. This level of accuracy is crucial for applications where parts need to fit together perfectly or meet stringent performance requirements. Because of the accuracy that CNC machining provides, you can confidently rely on the parts you create.
2. Design Flexibility: Unleashing Creativity
Aluminum CNC machining offers incredible design flexibility. Whether you need simple shapes or complex geometries, CNC machines can handle it all. This allows engineers and designers to unleash their creativity and develop innovative solutions without being limited by manufacturing constraints.
3. Rapid Prototyping: From Idea to Reality, Fast!
In today’s fast-paced world, speed is essential. Aluminum CNC machining is ideal for rapid prototyping, allowing you to quickly create prototypes of your designs to test form, fit, and function. This iterative process helps identify and correct any design flaws early on, saving time and money in the long run.
4. High Production Volume: Scaling Up with Ease
Once a design is finalized, aluminum CNC machining can be easily scaled up for high-volume production. The CNC machine can repeatedly produce parts with consistent quality, ensuring that you can meet the demands of your market.
5. Smooth Surface Finishes: Aesthetics Matter
Aluminum CNC machining can produce parts with very smooth surface finishes, which is crucial for applications where aesthetics are important. The smooth surface also provides a good base for coatings, paints, or other surface treatments.
6. Consistent Quality: Reliability You Can Count On
One of the most significant benefits of aluminum CNC machining is the consistent quality it delivers. The computer-controlled process eliminates the risk of human error, ensuring that each part is manufactured to the same high standards.
Cost-Effectiveness of Aluminum CNC Machining
When it comes to manufacturing, cost is always a significant consideration. Aluminum CNC machining offers several cost advantages that make it a highly competitive option.
1. Material Costs
Aluminum is generally less expensive than other materials like titanium or stainless steel. This lower material cost, combined with its recyclability, can lead to significant savings over the life of a product.
2. Machining Costs
Due to its machinability, aluminum can be processed faster and with less wear on cutting tools. This reduces machining time and tooling costs, making the overall process more affordable.
3. Reduced Waste
CNC machining is a subtractive process, where material is removed to create the desired shape. With aluminum, the chips and waste material are often valuable and can be recycled, reducing the overall cost of the process and minimizing environmental impact.
Versatility in Applications
The benefits of aluminum CNC machining are not limited to a single industry. Its versatility makes it suitable for a wide range of applications across various sectors.
1. Aerospace
In the aerospace industry, aluminum is used for aircraft parts, satellite components, and rocketry. Its lightweight and strong properties make it ideal for reducing fuel consumption and improving performance.
2. Automotive
The automotive industry relies heavily on aluminum to produce engine components, chassis parts, and body panels. Aluminum CNC machining helps create parts that are both lightweight and durable, contributing to better fuel efficiency and safety.
3. Electronics
For electronics, aluminum is used in heat sinks, enclosures, and connectors. Its excellent thermal and electrical conductivity, combined with its ability to achieve fine finishes, make it a preferred material for high-performance components.
4. Medical
In the medical industry, aluminum is used for surgical instruments, implants, and diagnostic equipment. Its biocompatibility, corrosion resistance, and precision make it a safe and reliable choice for medical applications.
5. Consumer Goods
Aluminum is also a favorite in the consumer goods industry, where it is used for products like laptop casings, watch components, and kitchenware. Its aesthetic appeal and durability make it a popular material for both functional and decorative items.
Comparison of Common Aluminum Alloys for CNC Machining
Aluminum Alloy | Properties | Common Applications | Machinability | Cost |
---|---|---|---|---|
6061 | – High strength – Good corrosion resistance – Easy to weld |
– Aircraft parts – Structural components – Electrical components |
Excellent | Moderate |
7075 | – Very high strength – Good fatigue resistance – Excellent machinability |
– Aerospace components – Bicycle frames – Defense equipment |
Very good | High |
2024 | – High strength – Good fatigue resistance – Good machinability |
– Aircraft structures – Military hardware |
Good | High |
5052 | – High corrosion resistance – Good workability – Moderate strength |
– Marine components – Chemical tanks |
Good | Moderate |
6063 | – Good extrudability – High corrosion resistance – Good machinability |
– Architectural applications – Window frames – Door frames |
Very good | Low |
Tips for Successful Aluminum CNC Machining
To get the most out of aluminum CNC machining, here are some tips to consider:
1. Choose the Right Alloy
Selecting the appropriate aluminum alloy for your project is crucial. Different alloys have different properties, and choosing the right one can improve the performance and cost-effectiveness of your parts.
2. Optimize Tooling
Using the right cutting tools and coolant can significantly enhance the machining process. For example, carbide tools are often preferred for aluminum due to their hardness and durability.
3. Consider Post-Machining Treatments
While aluminum can achieve excellent surface finishes, post-machining treatments like anodizing or painting can further enhance its properties. Anodizing, for instance, can improve corrosion resistance and add color to the parts.
4. Design for Machinability
When designing parts, consider the machinability of aluminum. Avoid complex geometries that may increase machining time and costs. Simplifying the design can lead to more efficient and cost-effective production.
5. Test and Iterate
For new projects, it’s always a good idea to create prototypes and test them. This allows you to refine the design and ensure that the parts meet all specifications before moving to full-scale production.
Frequently Asked Questions (FAQs)
1. What is the best aluminum alloy for CNC machining?
The best aluminum alloy depends on the specific requirements of your project. For general machining, 6061 and 7075 are popular choices due to their excellent machinability and high strength. However, for specific applications, other alloys like 2024, 5052, and 6063 may be more suitable.
2. How does aluminum CNC machining compare to other manufacturing methods?
Aluminum CNC machining offers higher precision and flexibility compared to methods like casting or forging. It is also more cost-effective for small to medium-sized production runs, as it requires less setup time and can produce complex geometries easily.
3. Can aluminum CNC parts be used in harsh environments?
Yes, aluminum parts can be used in harsh environments, especially when treated with processes like anodizing or painting. These treatments enhance corrosion resistance and durability, making aluminum parts suitable for applications in marine, chemical, and automotive industries.
4. What is the minimum wall thickness for aluminum CNC parts?
The minimum wall thickness for aluminum CNC parts typically ranges from 0.030 to 0.060 inches, depending on the alloy and the specific requirements of the part. However, it’s always best to consult with your CNC machining provider to ensure that the design is feasible.
5. Is aluminum CNC machining environmentally friendly?
Yes, aluminum CNC machining is environmentally friendly. Aluminum is 100% recyclable, and the chips produced during machining can be recycled and reused. Additionally, the process is more energy-efficient compared to other manufacturing methods, making it a sustainable choice.
Conclusion
Aluminum CNC machining is a versatile and cost-effective process that offers numerous benefits. From its lightweight and strong properties to its excellent thermal and electrical conductivity, aluminum is a material that can meet the demands of a wide range of industries. By understanding the advantages and tips for successful machining, you can leverage this technology to create high-quality, precision parts that meet your project’s requirements.
Whether you’re a seasoned manufacturer or a newcomer to the field, aluminum CNC machining is a process worth considering for your next project. Its combination of material properties, precision, and cost-effectiveness makes it a top choice in the manufacturing world. So, the next time you need to create a part, consider aluminum CNC machining and experience the benefits for yourself.
If you have any more questions or need further assistance, feel free to reach out or explore the FAQs above. Happy machining!