Choosing the right metal for your project can feel like navigating a minefield. Strength, weight, cost – so many factors to consider! Two popular contenders often emerge: titanium and aluminum. Both boast impressive qualities, but understanding their differences is crucial to making the best choice. As someone who’s worked with both metals, I’m here to break down their properties, advantages, and disadvantages to help you decide which one is right for you.
Titanium vs. Aluminum: Comparing Their Properties
Before diving into the specifics of each metal, let’s take a quick look at some key properties that often influence material selection.
Property | Titanium | Aluminum |
---|---|---|
Density | ~4.5 g/cm³ | ~2.7 g/cm³ |
Strength-to-Weight Ratio | Excellent | Good |
Corrosion Resistance | Excellent | Good (especially with alloys) |
Melting Point | ~1,668 °C (3,034 °F) | ~660 °C (1,220 °F) |
Cost | Higher | Lower |
Workability | More challenging to machine and form | Easier to machine and form |
Conductivity (Thermal & Electrical) | Lower | Higher |
Biocompatibility | Excellent | Good (Aluminum alloys varies) |
This table provides a quick overview, but let’s delve deeper into each metal to understand these properties in context.
An Overview of Titanium
Titanium, often referred to as a “space-age metal,” has garnered a reputation for its exceptional strength, lightweight nature, and remarkable corrosion resistance. It’s a naturally occurring element found in the Earth’s crust and is known for its silvery-white appearance.
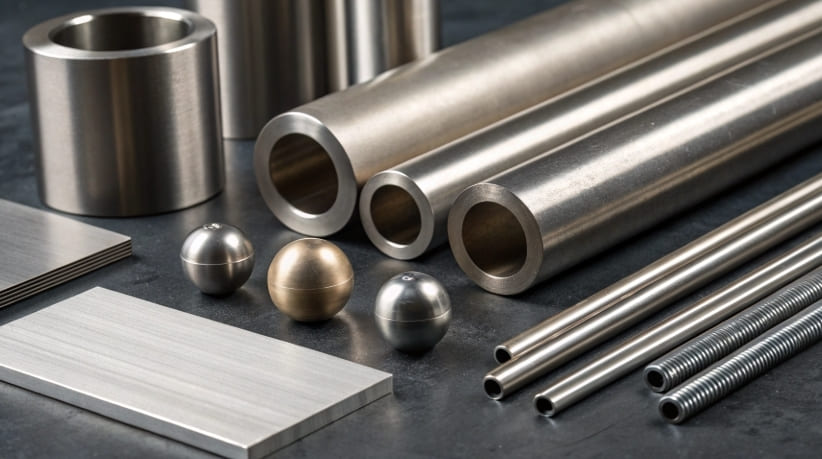
-
Key Advantages of Titanium:
- High Strength-to-Weight Ratio: This is where titanium truly shines. It’s as strong as many steels but significantly lighter, making it ideal for applications where weight is a critical factor.
- Exceptional Corrosion Resistance: Titanium forms a passive oxide layer when exposed to air, which protects it from corrosion in a wide range of environments, including seawater, acids, and chlorine.
- Biocompatibility: Titanium is non-toxic and doesn’t react with bodily fluids, making it ideal for medical implants and surgical instruments.
- High Melting Point: Its high melting point makes it suitable for high-temperature applications.
-
Key Disadvantages of Titanium:
- High Cost: Titanium is significantly more expensive than aluminum due to the complex extraction and processing methods required.
- Difficult Machinability: It’s harder to machine and form than aluminum, requiring specialized tools and techniques.
- Lower Thermal and Electrical Conductivity: Compared to aluminum, titanium doesn’t conduct heat or electricity as efficiently.
Common Applications of Titanium:
- Aerospace components (aircraft, spacecraft)
- Medical implants (hip replacements, dental implants)
- Sporting goods (golf clubs, bicycle frames)
- Chemical processing equipment
- Marine applications (shipbuilding, offshore platforms)
- Jewelry
An Overview of Aluminum
Aluminum is another widely used metal known for its lightweight properties, corrosion resistance, and versatility. It’s the third most abundant element in the Earth’s crust.

-
Key Advantages of Aluminum:
- Lightweight: Aluminum is significantly lighter than steel and titanium, making it ideal for applications where weight reduction is crucial.
- Good Corrosion Resistance: While not as corrosion-resistant as titanium, aluminum forms a protective oxide layer that prevents rust in many environments. Alloying aluminum with other elements can further enhance its corrosion resistance.
- Excellent Workability: Aluminum is easy to machine, form, and weld, making it a popular choice for a wide range of manufacturing processes.
- High Thermal and Electrical Conductivity: Aluminum is an excellent conductor of heat and electricity, making it suitable for applications like heat sinks and electrical wiring.
- Recyclable: Aluminum is highly recyclable without losing its properties, making it an environmentally friendly choice.
- Lower Cost: Aluminum is significantly cheaper than titanium.
-
Key Disadvantages of Aluminum:
- Lower Strength-to-Weight Ratio: Compared to titanium, aluminum is less strong for its weight.
- Lower Melting Point: Its lower melting point limits its use in high-temperature applications.
- Can be susceptible to certain types of corrosion: Under certain conditions like highly acidic or alkaline environments, aluminum can corrode.
Common Applications of Aluminum:
- Aerospace components (aircraft fuselages, wings)
- Transportation (cars, trains)
- Packaging (cans, foil)
- Construction (window frames, siding)
- Electrical transmission lines
- Cookware
Titanium Vs. Aluminum: Which Metal Should You Choose?
Now that we’ve explored the properties of both metals, let’s address the million-dollar question: Which one should you choose for your project? The answer depends entirely on your specific requirements and priorities. To help you make the best decision, consider these factors:
- Weight: If weight is the most critical factor and you need the absolute lightest option while maintaining strength, titanium is the winner. However, if weight is important but not the absolute top priority, aluminum provides a significant weight reduction compared to steel at a lower cost.
- Strength: If you need the highest possible strength-to-weight ratio, titanium is the clear choice.
- Corrosion Resistance: For extremely harsh environments, especially those involving seawater or strong chemicals, titanium’s superior corrosion resistance makes it the better option. However, for many applications, aluminum alloys offer adequate corrosion resistance.
- Cost: If budget is a major concern, aluminum is significantly more affordable than titanium.
- Machinability: If your project requires extensive machining or forming, aluminum is much easier to work with.
- Temperature: If your application involves high temperatures, titanium’s higher melting point makes it a more suitable choice.
- Conductivity: For electrical or thermal applications, aluminum’s superior conductivity makes it the better option.
Here’s a brief checklist for you:
-
- Choose Titanium if:
- You need the highest strength-to-weight ratio.
- Your project requires exceptional corrosion resistance.
- Weight is paramount, and cost is less of a concern.
- You need biocompatibility (e.g., for medical implants).
- Choose Aluminum if:
- You need a lightweight and cost-effective solution.
- Your project requires good corrosion resistance in typical environments.
- Machinability and formability are important.
- You need good thermal or electrical conductivity.
Conclusion
Both titanium and aluminum are remarkable materials with their own set of advantages and limitations. The choice between the two depends on the specific requirements of your project. By considering factors such as weight, corrosion resistance, biocompatibility, cost, and aesthetic appeal, you can make an informed decision that will ensure the success of your project.
If you’re looking for a material that combines strength, durability, and resistance to harsh environments, titanium is the way to go. On the other hand, if you need a lightweight, cost-effective, and versatile material, aluminum is the better choice. Whatever your project, I hope this guide has provided you with the insights you need to make the right decision.
FAQs
-
Is titanium stronger than aluminum?
Yes, titanium generally has a higher tensile strength than aluminum. However, it’s more accurate to consider the strength-to-weight ratio. Titanium offers superior strength for its weight.
-
Is titanium always better than aluminum?
No. While titanium has many advantages, it’s also more expensive and harder to work with. Aluminum is a better choice when cost, machinability, or conductivity are primary concerns.
-
Can aluminum replace titanium in aerospace applications?
In some cases, yes, but not always. Aluminum is used in many aerospace components where weight is a concern, but titanium is preferred for critical parts that require exceptional strength and corrosion resistance in extreme conditions.
-
Are there different grades of titanium and aluminum?
Yes, both titanium and aluminum come in various alloys with different properties. Choosing the right alloy is crucial for specific applications.