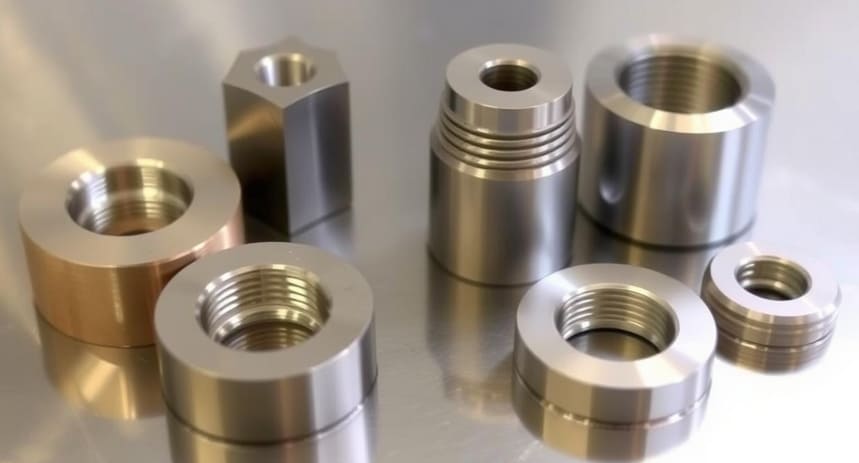
Titanium is often hailed as a wonder material, prized for its impressive strength-to-weight ratio, corrosion resistance, and biocompatibility. However, for those of us in the machining industry, titanium is not easy for machining. In this article, I’ll delve into what makes titanium so difficult to machine, exploring the unique properties of this metal and the challenges it presents. We’ll also look at some strategies to overcome these hurdles and provide a few frequently asked questions to help you better understand the complexities of working with titanium.
Why Choose Titanium?
Before we dive into the challenges, let’s talk about why titanium is so desirable in the first place. This metal is widely used in aerospace, medical, and automotive industries due to its exceptional properties:
- High Strength-to-Weight Ratio: Titanium boasts exceptional strength relative to its weight. This is why it’s favored in aerospace applications where minimizing weight is paramount. However, this also means it requires more force to cut and deform.
- Low Thermal Conductivity: Titanium doesn’t dissipate heat well. This is a huge problem during machining because the heat generated from cutting tends to concentrate at the cutting edge of the tool. This leads to rapid tool wear, work hardening of the material, and can even cause the titanium to weld itself to the cutting tool.
- High Chemical Reactivity: At elevated temperatures (which are easily reached during machining), titanium readily reacts with oxygen, nitrogen, and hydrogen in the air. This reactivity contributes to the formation of a hard, abrasive layer on the tool, accelerating wear.
- Low Elastic Modulus: Compared to steel, titanium has a lower elastic modulus. This means it’s more prone to spring back after being deformed. This “spring back” affects dimensional accuracy and makes it difficult to achieve tight tolerances.
- Corrosion Resistance: It forms a protective oxide layer that prevents further corrosion, which is why it’s used in marine and chemical processing environments.
- Biocompatibility: Titanium is non-toxic and non-reactive with human tissue, making it a go-to material for medical implants and surgical instruments.
However, these same properties that make titanium so valuable also make it a nightmare to machine. Let’s explore why.
The Challenges of Machining Titanium
1. Heat Generation
One of the primary challenges of machining titanium is the significant amount of heat it generates. Titanium has a low thermal conductivity, meaning it doesn’t dissipate heat well. This can lead to several issues:
- Tool Wear: The high temperatures can cause rapid tool wear, reducing the lifespan of cutting tools.
- Work Hardening: As the metal is cut, it can harden, making it even more difficult to machine and potentially leading to tool breakage.
- Material Degradation: Excessive heat can change the material properties of titanium, compromising the integrity of the final product.
2. Low Thermal Conductivity
As mentioned, titanium’s low thermal conductivity is a double-edged sword. While it’s great for applications where heat resistance is crucial, it makes machining a challenge. Here’s why:
- Cutting Speeds: You need to use lower cutting speeds to avoid overheating, which can increase machining time and costs.
- Coolant Use: Effective cooling is essential, but even with proper cooling, heat can build up quickly.
3. High Chemical Reactivity
Titanium is highly reactive with oxygen, nitrogen, and hydrogen at high temperatures. This reactivity can lead to:
- Tool Adhesion: Titanium can stick to the cutting tool, causing built-up edges (BUE) and reducing tool life.
- Surface Integrity: Reactivity can affect the surface finish, leading to micro-cracks and other defects that can compromise the part’s performance.
4. Low Modulus of Elasticity
Titanium has a low modulus of elasticity, which means it’s more flexible and can spring back during machining. This can result in:
- Vibration: The material’s flexibility can cause chatter and vibration, affecting the accuracy and finish of the machined part.
- Tool Deflection: Cutting tools can deflect, leading to inconsistent cuts and increased tool wear.
5. High Hardness and Strength
Titanium’s high hardness and strength are beneficial in many applications, but they make it challenging to machine. Here’s how:
- Tool Selection: You need to use more durable and harder cutting tools, such as those made from carbide or ceramics.
- Power Consumption: Machining titanium requires more power, which can increase energy costs and wear on machinery.
Strategies for Machining Titanium
Despite the challenges, titanium is still a highly sought-after material. Here are some strategies to help you machine it more effectively:
1. Use the Right Tools
- Carbide Tools: Carbide tools are more wear-resistant and can handle the high temperatures generated during machining.
- Ceramic Tools: For high-speed machining, ceramic tools can be a good option as they can withstand higher temperatures.
- Coated Tools: Tools with specialized coatings, such as titanium nitride (TiN) or diamond-like carbon (DLC), can improve wear resistance and reduce heat.
2. Optimize Cutting Parameters
- Lower Cutting Speeds: Reduce the cutting speed to prevent excessive heat generation.
- Higher Feed Rates: Increase the feed rate to help remove heat from the cutting zone.
- Depth of Cut: Use a shallower depth of cut to reduce the force required and minimize tool deflection.
3. Effective Cooling
- Flood Coolant: Use a flood coolant to keep the cutting zone as cool as possible. Common coolants include oil-based and water-soluble fluids.
- Mist Coolant: For smaller operations, mist coolant can be effective in reducing heat and improving surface finish.
4. Proper Machine Setup
- Rigid Machine: Ensure your machine is as rigid as possible to minimize vibration and deflection.
- Balanced Spindle: A balanced spindle can help reduce vibration and improve tool life.
- Secure Workholding: Use strong and secure workholding fixtures to prevent the workpiece from moving during machining.
5. Material Considerations
- Annealing: Annealing the titanium can reduce its hardness and make it easier to machine, but this must be done carefully to avoid changing its properties.
- Grain Structure: Choosing titanium with a finer grain structure can improve machinability and reduce tool wear.
A Closer Look at Titanium Grades
To better understand the challenges of machining titanium, it’s helpful to look at the different grades and their properties. The most common grades are:
Grade | Composition | Properties | Applications |
---|---|---|---|
1 | Commercially Pure | Soft, high formability | Chemical processing, medical devices |
2 | Commercially Pure | Balanced strength and formability | Aerospace, marine |
3 | Commercially Pure | Higher strength than Grade 2 | Aerospace, medical devices |
4 | Commercially Pure | Highest strength of all commercially pure grades | Aerospace, high-stress applications |
5 | Ti-6Al-4V | Most widely used grade, excellent strength and toughness | Aerospace, medical, automotive |
6 | Ti-6Al-4V ELI | Lower interstitial elements, higher purity | Medical implants, aerospace |
23 | Ti-6Al-4V + 0.5Fe | Improved machinability | Aerospace, automotive |
Each grade has its own set of machining challenges, but understanding these can help you choose the right grade for your specific application and optimize your machining process.
Comparing Machining Considerations: Titanium vs. Other Metals
To highlight the specific challenges posed by titanium, let’s compare it to some other common engineering materials:
Material | Thermal Conductivity | Tool Wear | Machining Speed | Chip Control |
---|---|---|---|---|
Steel | Moderate | Moderate | Moderate | Easier |
Aluminum | High | Low | High | Moderate |
Titanium | Low | High | Low | Difficult |
StainlessSteel | Low | High | Moderate | Difficult |
This table is a simple example, but it highlights the critical differences. Titanium’s low thermal conductivity and high reactivity directly contribute to tool wear and necessitate slower machining speeds.
The Future of Titanium Machining
Despite the challenges, advancements in technology are making titanium machining more efficient and cost-effective. These include:
- Improved Cutting Tool Materials and Coatings: New tool materials and coatings are constantly being developed to provide better wear resistance and heat dissipation.
- Advanced Machining Techniques: Techniques like high-speed machining (HSM) and cryogenic machining are being explored to improve titanium machinability.
- Simulation and Modeling: Computer simulations are being used to optimize cutting parameters and predict tool wear, reducing the need for costly trial-and-error experimentation.
FAQs About Machining Titanium
Q: Why is titanium so expensive to machine?
A: Titanium is expensive to machine because it requires specialized tools, lower cutting speeds, and more energy. The high heat generated during machining can also lead to rapid tool wear, increasing costs.
Q: Can titanium be machined with standard tools?
A: While it’s possible to machine titanium with standard tools, it’s not recommended. Using carbide or ceramic tools, or tools with specialized coatings, can significantly improve tool life and machining efficiency.
Q: How do I prevent work hardening when machining titanium?
A: To prevent work hardening, use lower cutting speeds and higher feed rates. Additionally, ensure your tools are sharp and that you’re using an effective coolant to keep the cutting zone cool.
Q: What are the best coolants for machining titanium?
A: Flood coolants, such as oil-based or water-soluble fluids, are typically the best choice for machining titanium. They help to dissipate heat and improve tool life.
Q: Can titanium be welded?
A: Yes, titanium can be welded, but it requires a controlled environment to prevent contamination. TIG welding is often preferred for titanium due to its precision and ability to create strong, clean welds.
Conclusion
Machining titanium is no easy task, but with the right tools, techniques, and understanding of the material’s properties, it can be done effectively. The key is to balance the need for precision and efficiency with the challenges posed by titanium’s unique characteristics. Whether you’re working on a high-stakes aerospace project or crafting a medical implant, taking the time to optimize your machining process can make all the difference. By following the strategies outlined in this article, you can tackle the titanium challenge head-on and produce high-quality parts with confidence.
So, the next time you’re faced with a titanium project, remember that while it may be a tough nut to crack, the results are well worth the effort. Happy machining!