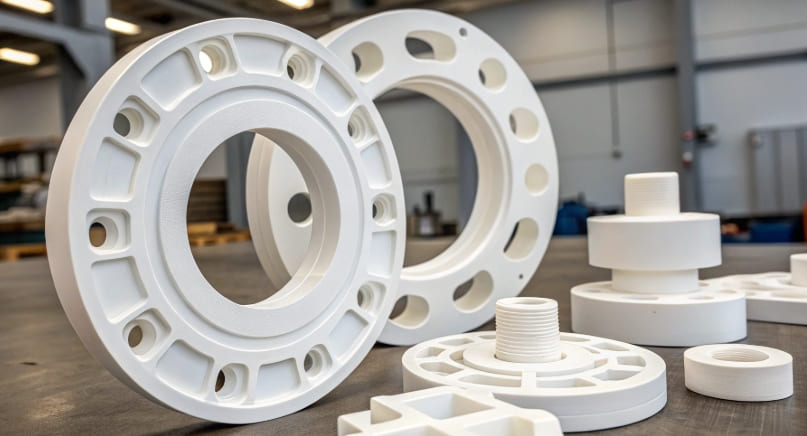
When it comes to part manufacturing, Teflon, also known as Polytetrafluoroethylene (PTFE), is a material that stands out for its unique properties. As someone who has worked extensively in the manufacturing and engineering industry, I can attest to the challenges and rewards of machining Teflon/PTFE. In this article, I’ll share my insights on the considerations and tips that can help ensure successful machining of this versatile material.
What is Teflon/PFTE Material?
Hello there! Today, we’re diving deep into the world of Teflon, also known as Polytetrafluoroethylene (PTFE). Teflon is a synthetic fluoropolymer of tetrafluoroethylene and is renowned for its remarkable properties. Coined by DuPont, Teflon has become a household name, but it’s also widely used in various industrial applications due to its unique characteristics.
Key Properties of Teflon/PTFE
- Non-Stick Surface: One of the most famous properties of Teflon is its non-stick surface, which makes it perfect for cookware and other applications where adhesion is undesirable.
- Low Friction: Teflon has one of the lowest coefficients of friction of any solid material, making it ideal for parts that require smooth, low-friction movement.
- Chemical Resistance: It is highly resistant to corrosion from chemicals, solvents, and even strong acids and bases.
- Temperature Range: Teflon can withstand a wide range of temperatures, from -200°C to 260°C, making it suitable for both cryogenic and high-heat environments.
- Dielectric Strength: It has excellent dielectric properties, which means it can be used in electrical insulation.
- Low Porosity: Teflon is nearly impermeable to gases and liquids, which helps in maintaining the integrity of components in various environments.
Different Machining Processes for Teflon/PTFE
Machining Teflon can be a bit tricky due to its softness and tendency to deform under pressure. However, there are several methods that can be used to create precise and high-quality parts.
1. Turning
Turning involves rotating the Teflon material while a cutting tool is used to remove material. This process is often used for creating cylindrical parts or parts with symmetrical features. Teflon’s low friction and deformation properties make it an excellent material for turning, but it requires careful tool selection and speed control to avoid damage.
2. Milling
Milling is a process where a rotating cutting tool is used to remove material from a stationary piece of Teflon. This method is suitable for creating complex shapes and intricate designs. Teflon’s softness means that it can be milled relatively easily, but it also requires precision to avoid chipping or tearing.
3. Drilling
Drilling is used to create holes in Teflon parts. It’s a straightforward process, but it requires the use of sharp tools to prevent the material from melting or deforming. The low melting point of Teflon means that drilling must be done at a slower speed to avoid overheating.
4. Cutting
Cutting Teflon can be done using various methods, including laser cutting, waterjet cutting, and knife cutting. Each method has its advantages, but laser cutting is particularly effective for creating precise and clean cuts without the risk of deformation.
5. EDM (Electrical Discharge Machining)
EDM is a non-traditional machining method that uses electrical discharges to remove material. This process is useful for creating intricate and detailed parts, but it can be more expensive and time-consuming compared to other methods.
Considerations and Tips for Machining Teflon
Now that we’ve covered the different machining processes, let’s dive into some important considerations and tips to ensure successful Teflon part manufacturing.
1. Material Selection
- Grade of PTFE: There are various grades of PTFE available, each with different properties. Choose the grade that best suits your application, considering factors like temperature resistance, mechanical strength, and chemical compatibility.
- Fillers and Additives: Sometimes, Teflon is mixed with fillers or additives to enhance specific properties. Common fillers include glass, carbon, and bronze. These can improve wear resistance, thermal conductivity, and mechanical strength.
2. Tool Selection
- Sharp Tools: Always use sharp tools to avoid tearing or deforming the Teflon material.
- High-Speed Steel (HSS) Tools: HSS tools are a good choice for machining Teflon because they can handle the material’s softness without excessive wear.
- Diamond-Coated Tools: For more precise and durable results, consider using diamond-coated tools. They can provide a smoother finish and longer tool life.
3. Speed and Feed Rates
- Slow Speeds: Teflon can deform if machined at high speeds. Use slower speeds to maintain the integrity of the material.
- Moderate Feed Rates: A moderate feed rate helps in achieving a smooth finish while preventing excessive heat buildup.
4. Cooling and Lubrication
- Coolant Use: While Teflon is generally machined dry, using a coolant can help in reducing heat and preventing deformation. However, choose a coolant that is compatible with Teflon to avoid any adverse reactions.
- Lubrication: If necessary, use a lubricant that is safe for Teflon. This can help in reducing friction and improving the finish.
5. Part Design
- Avoid Thin Walls: Teflon is relatively soft, so designing parts with thin walls can lead to deformation during machining. Aim for a minimum wall thickness of 1 mm to ensure stability.
- Tapered Features: Incorporating tapered features can help in easier ejection of parts from molds and better machining results.
Tips for Successful Teflon/PTFE Machining
Pre-Machining Preparation
- Material Quality: Ensure that the PTFE material you are using is of high quality. Low-quality PTFE can contain impurities that can affect machining performance.
- Tool Inspection: Before starting, inspect your tools for any signs of wear or dullness. A damaged tool can lead to poor results and wasted material.
- Clamp Setup: Set up your clamping system to provide even pressure without deforming the material. Soft jaw clamps or vacuum fixtures are ideal.
During Machining
- Start Slow: Begin with low cutting speeds and gradually increase as you become more comfortable with the material. This will help you gauge how the material reacts and make adjustments as needed.
- Frequent Tool Changes: Even with high-quality tools, expect to change them more frequently than you would with other materials. This will ensure that you maintain a sharp edge and achieve the best results.
- Monitor Temperature: Keep an eye on the temperature of the material and tools. If you notice excessive heat, reduce the cutting speed or increase the coolant flow.
- Regular Breaks: Take regular breaks to allow the material and tools to cool down. This can help prevent overheating and prolong tool life.
Post-Machining
- Inspection: After machining, inspect the parts for any signs of deformation, burrs, or other defects. PTFE can be prone to these issues, especially if the machining process is not carefully controlled.
- Cleaning: Clean the parts thoroughly to remove any coolant, chips, or debris. This is crucial for maintaining the material’s non-stick properties.
- Storage: Store machined PTFE parts in a clean, dry environment to prevent contamination and ensure their longevity.
Why CNC Machining is a Better Method for Manufacturing Teflon Parts?
CNC (Computer Numerical Control) machining is a highly precise and automated method for manufacturing parts. When it comes to Teflon, CNC machining offers several advantages over traditional methods.
1. Precision and Consistency
- High Tolerance: CNC machines can achieve very tight tolerances, which is crucial for parts that require precise dimensions.
- Repeatability: Once a design is programmed, CNC machines can produce multiple parts with consistent quality, which is ideal for high-volume production.
2. Versatility
- Complex Geometries: CNC machining can handle complex and intricate designs with ease, which is often challenging with traditional methods.
- Customization: CNC machines can be programmed to create custom parts, making them highly versatile for various applications.
3. Efficiency
- Automated Process: CNC machining reduces the need for manual intervention, which can speed up production and reduce labor costs.
- Reduced Waste: The precision of CNC machines means that there is less material waste, which is both cost-effective and environmentally friendly.
4. Surface Finish
- Smooth Finish: CNC machines can produce parts with a very smooth surface finish, which is especially important for applications where a non-stick surface is critical.
- Minimal Post-Processing: The high quality of CNC-machined parts often eliminates the need for additional post-processing steps, saving time and resources.
Application of PTFE Machined Parts
Teflon-machined parts have a wide range of applications across various industries due to their unique properties. Here are some common uses:
1. Aerospace
- Seals and Gaskets: Teflon’s chemical resistance and low friction make it ideal for seals and gaskets in aerospace applications.
- Electrical Insulation: Its dielectric properties are useful for insulating electrical components in aircraft.
2. Medical
- Implants and Instruments: Teflon’s biocompatibility and non-stick properties make it suitable for medical implants and instruments.
- Tubing and Valves: It is used in various medical devices, such as catheters and valves, due to its low friction and chemical resistance.
3. Automotive
- Bearings and Bushings: Teflon’s low friction and wear resistance make it a popular choice for bearings and bushings in automotive parts.
- Fuel System Components: Its chemical resistance and low porosity are beneficial for fuel system components that need to withstand harsh chemicals.
4. Food and Beverage
- Non-Stick Coatings: Teflon is widely used in cookware and food processing equipment for its non-stick properties.
- Seals and Valves: It is used in food and beverage processing to ensure cleanliness and prevent contamination.
5. Chemical Processing
- Piping and Fittings: Teflon’s chemical resistance makes it suitable for piping and fittings in chemical processing plants.
- Reactors and Vessels: It is used in reactors and vessels to prevent chemical reactions and maintain purity.
Common Challenges and Solutions
Material Deformation
- Challenge: PTFE is soft and can easily deform during machining, leading to parts that do not meet specifications.
- Solution: Use lower cutting speeds and softer clamping methods. Consider using a coolant to help dissipate heat and reduce the risk of deformation.
Tool Wear
- Challenge: PTFE is abrasive and can cause rapid wear on cutting tools, leading to increased costs and downtime.
- Solution: Use high-quality tungsten carbide tools and perform regular tool inspections. Frequent tool changes may be necessary to maintain a sharp edge.
Surface Finish
- Challenge: Achieving a smooth, high-quality surface finish on PTFE can be difficult due to its softness and tendency to chip.
- Solution: Use multiple finishing passes and low cutting speeds. Consider using a honing or polishing step to refine the surface finish.
Heat Generation
- Challenge: PTFE has low thermal conductivity, which means that heat generated during machining can build up and cause melting or deformation.
- Solution: Use a coolant to keep the material and tools cool. Monitor the temperature and adjust the cutting speed as needed to prevent overheating.
Case Study: Machining PTFE Seals for Aerospace Applications
To illustrate the practical application of these tips, let’s consider a case study where PTFE seals were machined for use in an aerospace application. The seals needed to meet strict dimensional tolerances and have a smooth, non-stick surface.
Project Overview
- Material: High-quality PTFE
- Tooling: Tungsten carbide end mills and drills
- Coolant: Light oil
- Clamping: Soft jaw clamps
- Machining Speeds: Low cutting speeds and feed rates
- Surface Finish: Multiple finishing passes with honing
Process
- Material Preparation: The PTFE stock was inspected for impurities and cut to the appropriate size.
- Tool Inspection: All tools were checked for sharpness and any signs of wear.
- Clamping Setup: Soft jaw clamps were used to securely hold the material without causing damage.
- Machining: The seals were machined using low cutting speeds and a light oil coolant. Multiple finishing passes were performed to achieve the desired surface finish.
- Inspection: Each seal was inspected for dimensional accuracy and surface finish. Any parts that did not meet specifications were reworked or discarded.
- Cleaning and Storage: The seals were cleaned thoroughly to remove coolant and debris and stored in a clean, dry environment.
Results
The project was a success, with all seals meeting the required specifications. The use of low cutting speeds, tungsten carbide tools, and a coolant helped prevent material deformation and tool wear. The multiple finishing passes ensured a smooth, non-stick surface, which is crucial for aerospace applications.
Alternative Materials to Teflon
While Teflon is an excellent material for many applications, there may be situations where alternative materials are more suitable. Here are some common alternatives:
1. PEEK (Polyether Ether Ketone)
- Properties: High strength, excellent wear resistance, and good chemical resistance.
- Applications: High-performance bearings, pistons, and other mechanical parts.
2. FEP (Fluorinated Ethylene Propylene)
- Properties: Similar to Teflon but with better UV resistance and a higher melting point.
- Applications: Outdoor and high-temperature applications.
3. PVDF (Polyvinylidene Fluoride)
- Properties: Strong, flexible, and resistant to a wide range of chemicals.
- Applications: Piping, tanks, and other industrial components.
4. Acetal (POM)
- Properties: High stiffness, low friction, and good dimensional stability.
- Applications: Gears, bearings, and other mechanical parts.
Conclusion
Machining Teflon/PTFE requires careful consideration of its unique properties and the appropriate use of tools and techniques. Whether you’re producing parts for the aerospace, medical, automotive, food and beverage, or chemical processing industries, Teflon’s non-stick, low-friction, and chemical-resistant properties make it a valuable material. CNC machining is particularly well-suited for Teflon due to its precision and efficiency. However, if Teflon isn’t the best fit for your application, there are several alternative materials to consider. Always consult with a material expert to ensure you choose the right material for your specific needs.
I hope this article has been helpful in understanding the considerations and tips for machining Teflon/PTFE parts. If you have any further questions, feel free to reach out!
FAQs
1. What is the melting point of Teflon/PTFE?
The melting point of Teflon/PTFE is around 327°C (621°F). This high melting point makes it suitable for a wide range of temperature applications.
2. Can Teflon be glued?
Yes, Teflon can be glued, but it requires special adhesives that are designed to bond with fluoropolymers. Common adhesives include cyanoacrylates and epoxies.
3. What are the common fillers used in Teflon?
Common fillers used in Teflon include glass, carbon, and bronze. These fillers can improve properties like wear resistance, thermal conductivity, and mechanical strength.
4. Is Teflon biocompatible?
Yes, Teflon is biocompatible and is widely used in medical applications, including implants and instruments.
5. What is the difference between Teflon and PTFE?
Teflon is a brand name for PTFE (Polytetrafluoroethylene) and is produced by DuPont. While the terms are often used interchangeably, Teflon is a specific type of PTFE with certain proprietary characteristics.