Material Selection Guide
GMetals offer custom machining services for a wide range of materials, including steel, aluminum, brass, copper, and more. Whatever your material needs, we provide tailored solutions to meet your specific requirements with precision and quality
Contact us if the material you need not show here
Stainless Steel
Stainless steel is a durable and corrosion-resistant material widely used in CNC machining and sheet metal fabrication. It comes in various grades, including 303, 304, 316, 410, 430, and more specialized grades like 17-4PH and 2205 duplex stainless steel. Grade 303 offers good machinability and corrosion resistance, suitable for complex parts. Grade 304 is known for its excellent corrosion resistance and weldability, making it suitable for kitchenware and medical equipment. Grade 316 offers superior resistance to acids and chlorides, ideal for marine and chemical applications. Grade 410 provides high strength and is often used for cutlery and tools. High-strength grades like 17-4PH are used in aerospace and military applications for their excellent mechanical properties. Stainless steel’s high tensile strength and aesthetic finish make it perfect for architectural elements, automotive components, and heavy-duty machinery.
Aluminum
Aluminum is a lightweight, corrosion-resistant metal that is easy to machine and highly versatile. Common grades include 2024, 5052, 6061, 6063, 7075, and specialized grades such as 5083 and 3003. Grade 2024 is known for its high strength, often used in aerospace structures. 5052 is highly resistant to corrosion, ideal for marine environments. Grade 6061 is popular for its good mechanical properties and weldability, suitable for structural components and automotive parts. 6063 is known for its smooth surface finish and is often used for architectural applications. Grade 7075 has a high strength-to-weight ratio, making it perfect for aerospace components. 5083 is commonly used for high-strength welded structures. Aluminum’s excellent heat dissipation makes it ideal for heat sinks and engine parts, and its adaptability and cost-effectiveness make it a staple in industries like construction, transportation, and packaging.
Brass
Brass, an alloy of copper and zinc, is known for its distinctive golden color and excellent machinability. It is available in different grades such as C260 (cartridge brass), C360 (free-machining brass), C280 (muntz metal), and C272 (yellow brass). C36000 offers superior machinability and durability, often used for precision components and fittings. C260 is valued for its strength and formability, making it suitable for decorative items, hardware, and ammunition casings. C280 is often used in marine and industrial applications due to its corrosion resistance. Brass is resistant to corrosion and exhibits good electrical conductivity, making it suitable for electrical components, musical instruments, and plumbing fittings. Its antimicrobial properties make it ideal for healthcare and food handling applications.
Titanium
Titanium is renowned for its high strength-to-weight ratio, exceptional corrosion resistance, and biocompatibility. Common grades include Grade 1, 2, 4, 5 (Ti-6Al-4V), 7, and Grade 9 (Ti-3Al-2.5V). Grade 1 offers excellent formability and corrosion resistance, ideal for chemical processing. Grade 2 is used for general industrial applications due to its good balance of strength and ductility. Grade 4 is the strongest of the commercially pure titanium grades, providing superior strength while maintaining good corrosion resistance, making it suitable for medical implants, marine components, and industrial equipment. Grade 5, the most common aerospace grade, provides high strength and heat resistance. Grade 7 has excellent corrosion resistance in aggressive environments. Grade 9 is used in aerospace and sports equipment due to its good weldability and strength. Titanium’s lightweight yet robust properties make it valuable in aerospace, military, and medical prosthetics. Its resistance to heat and environmental stressors ensures reliability in demanding conditions, such as chemical processing equipment.
Acrylic Material
Acrylic, also known as PMMA, is a transparent thermoplastic commonly used as a shatter-resistant alternative to glass. It comes in cast and extruded forms, each with different properties. Cast acrylic offers better optical clarity and chemical resistance, while extruded acrylic is more cost-effective and easier to machine. Acrylic provides high clarity, good impact resistance, and weatherability, making it suitable for applications like signage, displays, protective barriers, and light fixtures. Specialized types include UV-resistant acrylic and impact-modified acrylic for more demanding applications. Despite its brittleness compared to polycarbonate, it is lightweight and cost-effective, making it ideal for optical lenses, aquariums, and point-of-sale displays.
Carbon Steel
Carbon steel is a strong and durable material available in various grades, including low, medium, and high carbon. Grades such as A36, 1018, 1045, and specialized grades like 1095 and 8620 are commonly used. A36 is often employed in construction for its good weldability and strength. 1018 offers better machining capabilities and is suitable for parts requiring precise machining. 1045 has higher carbon content, providing increased hardness and strength, ideal for machinery and tools. High carbon steel such as 1095 is used for cutting tools due to its high hardness. Alloyed carbon steels like 8620 offer improved strength and case hardenability, ideal for gears and automotive components. Low carbon steel (mild steel) is easily weldable and used in automotive and structural applications, while high carbon steel is known for its hardness and wear resistance, perfect for cutting tools and springs.
POM Material
POM, or acetal, is an engineering thermoplastic known for its high strength, rigidity, and low friction. It is available in two main forms: homopolymer (e.g., Delrin) and copolymer. Homopolymer POM offers slightly higher mechanical properties, while copolymer POM provides better chemical resistance and dimensional stability. Variants such as glass-filled POM offer enhanced strength and rigidity. POM is highly machinable, making it suitable for precision parts such as gears, bearings, bushings, and fasteners. Its resistance to wear and high dimensional stability make it popular in automotive, industrial, and consumer electronics applications, where metal replacements are needed for weight reduction while maintaining performance.
Copper
Copper is a highly conductive and malleable metal used extensively in electrical and thermal applications. Common grades include C101 (oxygen-free copper), C110 (electrolytic tough pitch), C122 (phosphorous deoxidized copper), and C145 (tellurium copper). C101 provides maximum conductivity and is used in high-performance applications. C110 is the most commonly used grade for electrical wiring and components. C122 is used in plumbing and HVAC systems for its enhanced weldability. C145 offers good machinability while maintaining high conductivity, suitable for precision electronic parts. Copper’s high ductility allows for complex shaping, making it suitable for heat exchangers and decorative art. Its antimicrobial properties make it valuable for medical instruments and HVAC systems.
Tube Material
Metal tubes are hollow cylindrical structures made from materials such as stainless steel (304, 316), aluminum (6061, 6063), and copper (C110, C122). Stainless steel tubes are available in seamless and welded forms, suitable for high-pressure and corrosion-resistant environments like chemical processing and oil pipelines. Aluminum tubes are lightweight and corrosion-resistant, making them ideal for aerospace, automotive, and construction applications. Specialized types like anodized aluminum tubes offer additional corrosion resistance. Copper tubes are commonly used for plumbing and HVAC due to their excellent heat conductivity and formability. These tubes come in various diameters and wall thicknesses, essential for fluid conveyance and structural applications.
Plastic Material
Plastics are versatile, cost-effective materials used across numerous industries. Types like ABS, polycarbonate (PC), polyethylene (PE), nylon (PA), and specialized plastics like PTFE (Teflon) and PEEK each offer unique properties. ABS is tough and impact-resistant, suitable for automotive parts and electronic housings. Polycarbonate is highly durable and used for safety goggles and machine guards. Polyethylene comes in HDPE and LDPE forms, with HDPE offering higher strength, used in containers and pipes. Nylon’s strength and abrasion resistance make it ideal for mechanical components and gears. PTFE is used in high-temperature and chemical-resistant applications. PEEK offers superior mechanical properties and heat resistance, used in medical devices and aerospace components. Plastics are essential in consumer goods, automotive interiors, and electronics due to their lightweight and insulating properties.
Iron
Iron, a fundamental material in manufacturing, is valued for its strength and availability. It is commonly alloyed to create cast iron (e.g., gray iron, ductile iron) and wrought iron. Gray iron, known for its good vibration damping and machinability, is used in engine blocks and heavy machinery. Ductile iron provides better impact and fatigue resistance, suitable for automotive and industrial applications. Wrought iron, with its malleability and corrosion resistance, is used in decorative applications, gates, and fences. Specialized forms like malleable iron offer enhanced toughness. Iron’s strength-to-cost ratio makes it a cornerstone in construction and industrial equipment, though it requires protective coatings to prevent rust.
Beryllium Copper
Beryllium copper is a non-ferrous alloy known for its excellent strength, conductivity, and fatigue resistance. Common grades include C17200 (alloy 25), C17300, and C17510. C17200 offers high hardness and tensile strength, making it ideal for springs, connectors, and precision instruments. C17300 contains a small amount of lead to enhance machinability while maintaining high performance, suitable for precision components. C17510 is used for applications requiring excellent electrical conductivity, such as switch contacts and connectors. Beryllium copper is also known for its non-sparking properties, making it valuable in oil and gas equipment and other hazardous environments.
Carbon Fiber
Carbon fiber is a high-strength, lightweight material made from thin carbon filaments woven into fabric and bonded with resin to form composite structures. Types include standard modulus, intermediate modulus, and high modulus carbon fiber. Standard modulus is versatile and widely used in automotive, sports equipment, and industrial applications for its good balance of strength and flexibility. Intermediate modulus offers increased strength and stiffness, commonly used in aerospace and precision engineering. High modulus carbon fiber provides the highest stiffness, ideal for specialized applications like aircraft and satellite components. Carbon fiber’s excellent strength-to-weight ratio and low thermal expansion make it essential for high-performance, lightweight designs.
Bronze
Bronze is an alloy primarily composed of copper and tin, with variants such as phosphor bronze (C51000) and aluminum bronze (C95400). Phosphor bronze is known for its strength, fatigue resistance, and low friction, making it suitable for springs, bushings, and bearings. Aluminum bronze provides enhanced strength and corrosion resistance, commonly used in marine and heavy industrial applications. Bronze’s inherent resistance to saltwater corrosion makes it ideal for ship fittings and propellers. It is also popular in the art world for sculptures due to its beautiful finish and durability.
ABS Material
ABS (Acrylonitrile Butadiene Styrene) is a popular thermoplastic polymer known for its excellent balance of strength, durability, and processability. ABS materials come in various types and grades, including standard, flame-retardant, heat-resistant, and impact-modified versions, each suited to specific applications. Key properties include high impact resistance, good mechanical strength, and moderate chemical resistance, with a melting temperature typically ranging from 220–260°C.
The versatility of ABS allows it to be used in a wide range of industries. It is frequently applied in automotive parts, electronic housings, consumer goods, and 3D printing due to its ease of molding and strong finish. Heat-resistant grades are ideal for components that need to withstand higher temperatures, while flame-retardant versions are crucial in electrical and safety-focused applications. Impact-modified ABS enhances durability, making it suitable for products like helmets and protective gear.
Contact us freely
You have questions? We are available for you
Pls kindly fill out this form to receive more detailed information
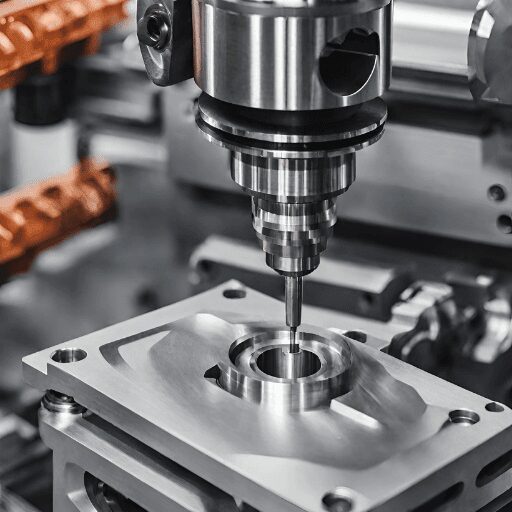