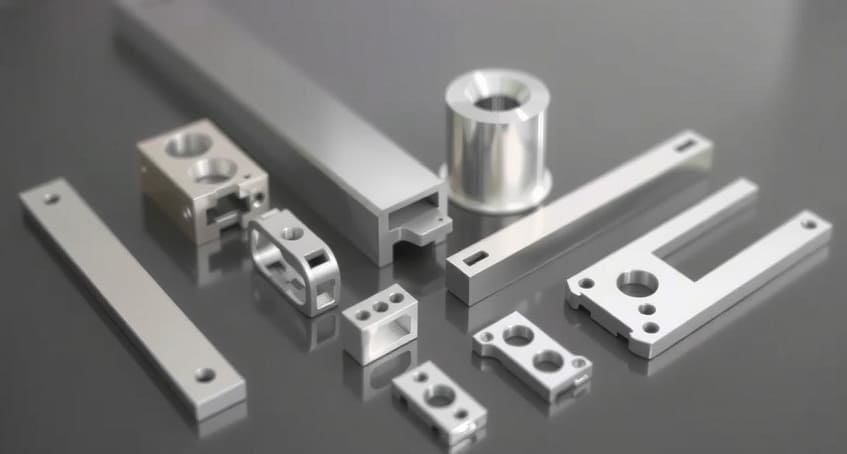
When it comes to precision manufacturing, CNC (Computer Numerical Control) machining is a go-to method for creating intricate and high-quality parts. One of the most commonly used materials in CNC machining is aluminum. But how much does it cost to CNC machine aluminum, and how does it compare to other materials? In this article, I’ll break down the costs, explore ways to lower them, and highlight the benefits of machining aluminum.
Introduction to CNC Machining Aluminum
CNC (Computer Numerical Control) machining is a manufacturing process where pre-programmed software controls the movement of machinery. When it comes to aluminum, CNC machining offers unparalleled precision, speed, and repeatability. Aluminum is a versatile material known for its lightweight, strength, and excellent thermal and electrical conductivity, making it ideal for a wide range of applications, from aerospace to automotive and consumer electronics.
Key Factors Influencing the Cost of CNC Machining Aluminum
Think of the price of your aluminum part as a recipe. Here are the main ingredients that go into the final cost:
1. Material Costs:
- Aluminum Grade: Different grades of aluminum have different prices. Common grades like 6061 are generally more affordable, while specialized alloys like 7075 (known for its high strength) will cost more.
- Quantity Needed: You’ll usually pay a premium for small quantities as suppliers often have minimum order requirements. Ordering larger volumes generally reduces the per-unit material cost.
- Material Source: Where the CNC shop sources their aluminum can also influence the price.
2. Design Complexity:
This is where things get interesting! The complexity of your design has a HUGE impact on the cost.
- Geometry: Parts with intricate curves, complex pockets, tight tolerances, and deep cavities require more machining time and expertise. Simple shapes, on the other hand, are quicker and easier to produce, resulting in lower costs.
- Tolerances: Requiring extremely tight tolerances (the allowable variation in dimensions) increases machining time and the need for specialized tooling and inspection. Looser tolerances are, naturally, cheaper.
- Surface Finish: If you need a specific surface finish (like a polished or anodized finish), that adds to the cost due to extra processing steps.
3. Machining Time:
This is a big one! CNC machines aren’t cheap to run, and machining time directly translates to labor costs.
- Part Size: Larger parts naturally take longer to machine.
- Material Removal Rate: Aggressive material removal can be faster, but it might compromise surface finish or accuracy. Slower, more controlled material removal takes more time but allows for greater precision.
- Number of Operations: Parts that require multiple setups (re-positioning the part in the machine) increase machining time.
4. Setup Costs:
Before the machining even begins, there’s setup work involved!
- Programming: CNC machines need to be programmed with specific instructions to create your part. This takes time and expertise, especially for complex designs.
- Tooling: The CNC shop will need appropriate cutting tools for your aluminum grade and geometry. Specialized or custom tools will add to the cost.
- Fixturing: Holding your part securely during machining is crucial. Custom fixtures can be expensive, but may be necessary for complex or delicate parts.
5. Quantity:
This seems obvious, but it’s worth emphasizing.
- Economies of Scale: As with most manufacturing processes, you’ll benefit from economies of scale. The more parts you order, the lower the per-unit cost will be because setup costs are distributed across a larger production run.
6. Finishing and Post-Processing:
- Deburring: Removing sharp edges (burrs) after machining is often necessary.
- Surface Finishing: As mentioned earlier, processes like anodizing, powder coating, or painting add to the cost.
- Inspection: Quality control and inspection are vital to ensure your part meets specifications. More rigorous inspection processes will increase costs.
Estimating the Cost: A Practical Approach
Okay, so how do you actually get a ballpark figure? Here’s my recommended approach:
- Prepare a Detailed Design (CAD Model): A accurate 3D CAD model is essential. This will help the CNC shop understand your requirements.
- Gather All Specifications: List all the important details such as aluminum grade, dimensions, tolerances, surface finish, and quantity.
- Contact Multiple CNC Shops: Don’t settle for the first quote you receive! Reach out to several CNC shops and ask for quotes based on your design and specifications. Be prepared to provide your CAD model and answer their questions.
- Compare Quotes Carefully: Don’t just look at the bottom line! Understand what’s included in each quote. Are there separate charges for setup, programming, or finishing?
- Ask Questions: Don’t be afraid to ask the CNC shop questions about their processes, tooling, and quality control procedures. This will help you choose a reliable partner.
Cost Comparison with Other Materials
Material | Average Cost per Hour | Notes |
---|---|---|
Aluminum | $50 – $200 | Versatile, lightweight, and cost-effective. |
Steel | $60 – $250 | Stronger and more durable, but heavier and more expensive. |
Titanium | $150 – $400 | Extremely strong and lightweight, but very expensive. |
Plastic | $30 – $150 | Lightweight and easy to machine, but less durable. |
Aluminum is generally more cost-effective than materials like titanium and steel, making it a popular choice for a wide range of applications, from aerospace to consumer electronics.
Tips to Manage CNC Machining Costs
-
Optimize Design for Manufacturability
- Simplify Geometry: Avoid unnecessary complexity in your design. Simplifying the geometry can reduce machining time and cost.
- Use Standard Tolerances: Unless absolutely necessary, avoid specifying extremely tight tolerances, which can significantly increase the cost.
-
Choose the Right Material
- Select Cost-Effective Grades: Grades like 6061 are generally more cost-effective than high-performance grades like 7075.
- Consider Material Thickness: Use the minimum thickness required for your application to reduce material costs.
-
Leverage Economies of Scale
- Order in Batches: Larger quantities can often reduce the per-unit cost due to lower setup and programming time.
- Combine Orders: If possible, combine multiple parts into a single order to save on setup costs.
-
Negotiate with Suppliers
- Get Multiple Quotes: Compare quotes from different CNC machining services to find the best value.
- Discuss Cost-Saving Options: Some suppliers may offer suggestions to reduce costs without compromising quality.
-
Consider Post-Processing
- Minimize Finishing Steps: Only include finishing processes that are essential for your application.
- Choose Cost-Effective Finishes: Anodizing is generally more cost-effective than painting or plating.
Benefits of Aluminum Machining
Aluminum is a popular choice for CNC machining for several reasons:
1. Lightweight and Strong
Aluminum is about one-third the weight of steel, making it ideal for applications where weight is a critical factor. Despite its lightweight, aluminum is also strong and durable, offering excellent strength-to-weight ratio.
2. Corrosion Resistance
Aluminum naturally forms a protective oxide layer, making it highly resistant to corrosion. This property makes it suitable for outdoor and marine applications.
3. Excellent Thermal and Electrical Conductivity
Aluminum is a good conductor of heat and electricity, making it ideal for use in electronics, heat sinks, and other thermal management applications.
4. Versatility
Aluminum can be easily machined, cast, forged, and extruded, making it a versatile material for a wide range of applications.
5. Cost-Effective
Compared to other materials like titanium and steel, aluminum is generally more affordable, making it a cost-effective choice for many projects.
FAQs
1. What is the most common aluminum alloy used in CNC machining?
The most common aluminum alloy used in CNC machining is 6061 aluminum. It is known for its good mechanical properties, ease of machining, and affordability.
2. How can I reduce the cost of CNC machining aluminum?
To reduce the cost, you can simplify part designs, choose cost-effective aluminum alloys, order in larger quantities, and shop around for the best prices.
3. Is aluminum machining suitable for all types of projects?
Aluminum machining is suitable for a wide range of projects, from small prototypes to large production runs. However, the suitability depends on the specific requirements of your project, such as strength, weight, and finish.
4. How does the cost of aluminum machining compare to steel machining?
Aluminum machining is generally more cost-effective than steel machining due to its lighter weight and easier machinability. However, the exact cost can vary based on the specific project requirements.
5. Can aluminum parts be anodized?
Yes, aluminum parts can be anodized to improve their corrosion resistance, wear resistance, and aesthetic appearance. Anodizing is a common finishing process for aluminum parts.
Conclusion
CNC machining aluminum is a cost-effective and versatile solution for a wide range of manufacturing needs. By understanding the factors that affect the cost and implementing strategies to reduce it, you can ensure that your project stays within budget while delivering high-quality results. Whether you’re working on a small prototype or a large production run, aluminum machining offers a combination of strength, durability, and cost-effectiveness that is hard to beat.
If you have any more questions or need further assistance, feel free to reach out. Happy machining!