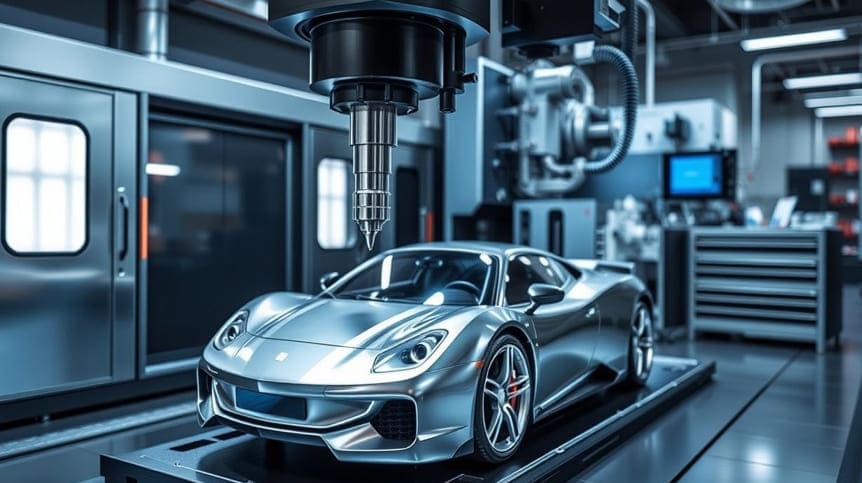
CNC machining, or Computer Numerical Control machining, is a game-changer in the manufacturing industry, especially in the automotive sector. As a professional writer with a keen interest in industrial technology, I’ve had the privilege of witnessing how this advanced method has revolutionized the way we produce and design vehicles. In this article, I’ll delve into the intricacies of CNC machining, its transformative impact on the automotive industry, its applications, limitations, and the exciting future that lies ahead.
What is CNC Machining?
CNC machining is a manufacturing process that uses pre-programmed computer software to control the movement of machinery and tools. Unlike manual manufacturing, where human operators control the machinery, CNC machining automates the process, ensuring precision, consistency, and efficiency. This technology can be applied to a variety of materials, including metals, plastics, and composites, making it incredibly versatile.
The process begins with a digital design created using Computer-Aided Design (CAD) software. This design is then converted into a set of instructions, or code, using Computer-Aided Manufacturing (CAM) software. The code is uploaded to the CNC machine, which executes the instructions to cut, shape, and form the material into the desired part or component.
CNC machining can be used for tasks ranging from simple drilling and cutting to complex 3D milling and turning. The machines can work around the clock, reducing production time and increasing output, which is particularly beneficial for high-volume manufacturing industries like automotive.
The Evolution of Automotive Manufacturing
The automotive industry has a rich history of innovation, from the early days of manual assembly lines to the highly automated processes we see today. One of the most significant technological advancements in recent years has been the integration of CNC machining. This technology allows for the precise and consistent production of components, from engine parts to interior pieces, using computer-controlled machinery.
From Manual to Digital
Before CNC machining, the manufacturing of automotive parts was largely a manual process. Skilled laborers would use hand tools and machines to create parts, which often led to variations in quality and fit. These manual methods were time-consuming and prone to human error. With CNC machining, the process became digital, with machines following precise instructions programmed by engineers. This shift not only improved the accuracy of parts but also significantly increased production speeds.
The Role of CNC in Modern Automotive Plants
In a modern automotive plant, CNC machines are everywhere. From the initial prototyping stages to the final assembly, these machines play a crucial role in ensuring that every part meets the exact specifications required. CNC machining has enabled automotive manufacturers to produce parts with higher precision, tighter tolerances, and greater consistency, which are essential for the performance and safety of vehicles.
How CNC Machining Transformed the Automotive Sector
The automotive industry has always been at the forefront of technological innovation. The introduction of CNC machining has significantly transformed how vehicles are manufactured, making the process more efficient, precise, and cost-effective. Here are some key ways in which CNC machining has revolutionized the automotive sector:
1. Increased Precision and Accuracy
CNC machines can achieve levels of precision that are nearly impossible with manual methods. This is crucial for automotive parts, where even the slightest deviation can affect the performance and safety of a vehicle. For example, engine components, such as pistons and cylinders, require precise dimensions to ensure optimal performance.
2. Enhanced Productivity
CNC machines can operate 24/7 without the need for breaks, significantly increasing productivity. This is particularly beneficial for large-scale automotive manufacturers who need to produce thousands of parts daily. The automation also reduces the likelihood of human error, leading to fewer reworks and higher quality standards.
3. Cost Reduction
While the initial investment in CNC machines can be high, the long-term cost savings are substantial. The ability to produce parts quickly and accurately reduces material waste and labor costs. Additionally, CNC machines can handle multiple tasks, reducing the need for specialized equipment and personnel.
4. Customization and Flexibility
CNC machining allows for greater customization and flexibility in design. Automotive manufacturers can easily modify designs and produce custom parts without the need for new tooling. This is particularly useful for small batch production and prototyping, where traditional methods would be less efficient and more expensive.
5. Improved Safety
The automation of the manufacturing process also enhances safety. CNC machines can handle dangerous tasks, such as cutting and drilling, with minimal human intervention, reducing the risk of workplace injuries.
Materials Matter: CNC Machining Handles Them All
The automotive industry utilizes a wide range of materials, each with its unique properties and requirements. From lightweight aluminum alloys to high-strength steel and durable plastics, CNC machining can handle them all. Different cutting tools and techniques are employed depending on the material, ensuring efficient and accurate machining.
Here’s a quick look at how CNC machining processes different materials commonly used in automotive manufacturing:
Material | CNC Process | Advantages |
---|---|---|
Aluminum Alloys | Milling, Turning, Drilling | Lightweight, corrosion resistant, excellent machinability |
Steel | Milling, Turning, Broaching, Grinding | High strength, durability, wear resistance |
Plastics | Milling, Routing, Turning | Lightweight, cost-effective, wide range of properties |
Composites | Ultrasonic Cutting, Waterjet Cutting, Milling | High strength-to-weight ratio, corrosion resistance, design flexibility |
This versatility allows manufacturers to choose the best material for each component without being limited by machining capabilities.
Applications of CNC Machining in the Automotive Sector
CNC machining has found numerous applications in the automotive industry, from the production of critical engine parts to the fabrication of interior components. Here are some of the most common applications:
1. Engine Components
- Cylinder Heads and Blocks: CNC milling machines are used to create the intricate shapes and channels required for cylinder heads and blocks.
- Pistons and Rings: CNC lathes ensure the precise dimensions and smooth surfaces needed for pistons and piston rings.
- Crankshafts and Camshafts: These critical components are often produced using CNC turning and milling, which ensures the high accuracy required for engine performance.
2. Transmission Parts
- Gearboxes: CNC machines are used to mill and turn the gears and shafts that make up the transmission system.
- Clutch and Brake Components: CNC machining ensures that clutch discs, brake pads, and other components are manufactured to exact specifications.
3. Suspension and Steering Parts
- Shock Absorbers: CNC machines can produce the intricate parts of shock absorbers with high precision.
- Steering Columns and Knuckles: CNC machining allows for the creation of complex shapes and precise dimensions in steering parts.
4. Exterior and Interior Components
- Body Panels: CNC routers and plasma cutters are used to shape and cut body panels from sheet metal.
- Interior Trim: CNC machines can create the intricate shapes and patterns found in dashboards, door panels, and other interior components.
5. Prototyping and Development
- Concept Cars: CNC machining is often used to create prototypes of new car designs, allowing manufacturers to test and refine their concepts before mass production.
- R&D: Automotive engineers use CNC machines to develop and test new materials and components, which can lead to innovations in vehicle performance and efficiency.
Limitations of CNC Machining in the Automotive Sector
While CNC machining offers numerous benefits, it also has some limitations that automotive manufacturers must consider:
1. High Initial Costs
The cost of purchasing and maintaining CNC machines can be prohibitive for smaller automotive companies. The initial investment includes not only the machines themselves but also the software, training, and infrastructure required to support them.
2. Complexity of Setup
Setting up a CNC machine for a new part or component can be time-consuming and requires skilled operators. The process involves creating a digital design, converting it to code, and ensuring the machine is properly calibrated.
3. Material Constraints
While CNC machines can work with a wide range of materials, some materials, such as certain composites and high-strength alloys, can be challenging to machine. These materials may require specialized tools and techniques, which can increase production costs.
4. Environmental Impact
CNC machining can generate a significant amount of waste material, which can be difficult to dispose of in an environmentally friendly manner. coolant and lubricants used in the machining process can also have environmental impacts if not properly managed.
5. Technological Dependence
The reliance on technology means that any software or hardware issues can halt production. Regular maintenance and updates are essential to keep the machines running smoothly.
The Future of CNC Machining in the Automotive Sector
The automotive industry is continually evolving, and CNC machining is no exception. As technology advances, we can expect to see even more innovative applications of CNC machining in the future. Here are some trends and predictions:
1. Integration with AI and Machine Learning
AI and machine learning are increasingly being integrated into CNC machining processes. These technologies can optimize machine settings, predict maintenance needs, and even improve the design of parts. This will lead to even greater efficiency and precision in manufacturing.
2. Additive Manufacturing (3D Printing)
The combination of CNC machining and 3D printing is becoming more common. 3D printing can create complex shapes and structures that are then refined using CNC machining. This hybrid approach can reduce material waste and production time, making it a promising development for the automotive industry.
3. Multi-Axis Machining
Multi-axis CNC machines are becoming more advanced, allowing for the creation of complex 3D parts with greater ease. This will enable automotive manufacturers to produce more intricate and lightweight components, which can improve vehicle performance and fuel efficiency.
4. Sustainability
As environmental concerns become more pressing, CNC machining will play a role in making the automotive industry more sustainable. Advances in tooling and machining techniques will reduce material waste, while the use of eco-friendly coolants and lubricants will minimize the environmental impact of the process.
5. Global Supply Chain Optimization
CNC machining can help optimize global supply chains by allowing for on-demand production and local manufacturing. This can reduce transportation costs and lead times, making the automotive industry more agile and responsive to market demands.
Conclusion
CNC machining has been a driving force behind the modernization of the automotive industry. Its ability to produce high-precision parts, enhance productivity, and reduce costs has made it an indispensable tool for automotive manufacturers. While there are some limitations to the technology, the future looks promising with the integration of AI, 3D printing, and sustainable practices. As the automotive industry continues to evolve, CNC machining will play a crucial role in shaping the vehicles of tomorrow.
Whether you’re a seasoned industry professional or a curious enthusiast, the impact of CNC machining on the automotive sector is undeniable. It’s a technology that not only meets the demands of modern manufacturing but also opens up new horizons for innovation and sustainability.
Feel free to reach out if you have any questions or need further information on how CNC machining is shaping the automotive industry!
FAQs
1. What is the difference between CNC machining and traditional machining?
- CNC machining uses computer software to control the machining process, ensuring high precision and consistency. Traditional machining relies on human operators, which can lead to variations and errors.
2. Can CNC machines be used for mass production in the automotive industry?
- Yes, CNC machines are well-suited for mass production due to their ability to work continuously and produce parts with consistent quality.
3. How does CNC machining contribute to the development of electric vehicles?
- CNC machining can produce the precision parts needed for electric vehicle components, such as battery casings, motor housings, and cooling systems, ensuring optimal performance and safety.
4. What types of materials are commonly used in CNC machining for automotive parts?
- Common materials include aluminum, steel, titanium, and various plastics and composites. Each material has its own properties and machining requirements.
5. Are there any environmental concerns with CNC machining in the automotive industry?
- Yes, material waste and the use of coolants and lubricants can have environmental impacts. However, advancements in technology are making the process more sustainable.