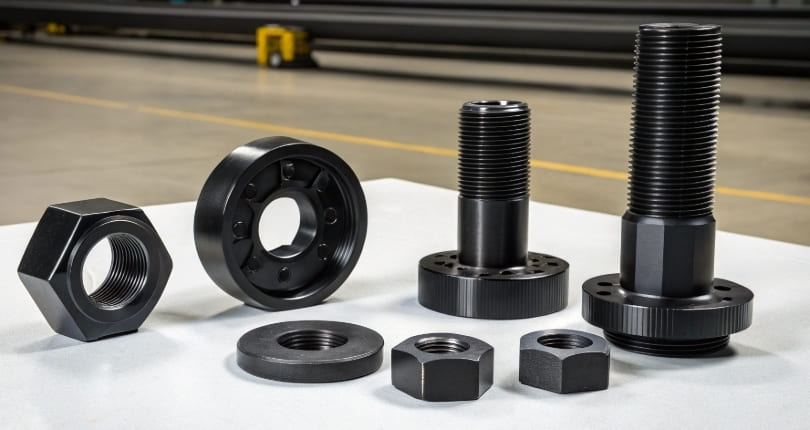
When it comes to enhancing the durability, aesthetics, and functionality of precision machined parts, black oxide coating is a standout process. As an engineer, I’ve seen firsthand how this simple yet effective technique can transform materials, making them more resistant to corrosion and wear. In this guide, I’ll walk you through the ins and outs of black oxide coating, from its history and chemistry to its applications and benefits. By the end, you’ll have a comprehensive understanding of why this finish is a go-to choice for many industries.
What is Black Oxide Coating?
Black oxide coating, also known as blackening or oxidizing, is a chemical conversion process that forms a black oxide layer on the surface of metals. This layer is not a paint or a plating but a reaction between the metal and the chemicals used in the process. The result is a thin, uniform, and durable finish that offers several advantages over other surface treatments.
History of Black Oxide Coating
The origins of black oxide coating can be traced back to the early 20th century when it was first used in the firearms industry. The process was adopted to reduce glare and improve the aesthetics of guns. Over time, its applications expanded to include automotive, aerospace, and medical industries, where it is valued for its protective and decorative properties.
Chemistry Behind Black Oxide Coating
The black oxide coating process involves immersing the metal part in a solution of alkaline salts and water. The metal reacts with the solution, forming a layer of magnetite (Fe3O4) on the surface. This layer is typically about 0.00005 to 0.0001 inches thick, which is much thinner than traditional paint or plating.
The process can be summarized in three main steps:
- Cleaning: The metal part is thoroughly cleaned to remove any oils, greases, or contaminants that could interfere with the coating.
- Blackening: The part is immersed in the black oxide solution, where the chemical reaction takes place.
- Rinsing and Drying: The coated part is rinsed to remove any residual chemicals and then dried to prevent rusting.
Benefits of Black Oxide Coating
Corrosion Resistance
One of the primary benefits of black oxide coating is its ability to provide a barrier against corrosion. While the black oxide layer itself is not highly resistant to rust, it helps to seal the surface of the metal, reducing the likelihood of moisture and air coming into contact with the underlying material. This makes it particularly useful for parts that are exposed to moderate environmental conditions.
Aesthetic Appeal
Black oxide coating gives metal parts a sleek, uniform, and professional appearance. It is often used in applications where a dark, matte finish is desired, such as in firearms, watches, and high-end automotive components. The finish is also less reflective than other coatings, which can be beneficial in reducing glare in certain environments.
Wear Resistance
The black oxide layer is hard and durable, providing enhanced wear resistance. This is particularly important for parts that undergo frequent use or are exposed to abrasive conditions. The coating can help extend the lifespan of these parts, making it a cost-effective solution in the long run.
Dimensional Stability
Unlike paint or other surface treatments, black oxide coating does not significantly alter the dimensions of the part. This makes it ideal for precision machined components where maintaining tight tolerances is crucial.
Cost-Effective
Black oxide coating is generally more affordable than other surface treatments like electroplating or painting. It requires less equipment and fewer steps, which can translate to lower production costs.
Lubrication Improvement
The black oxide finish can improve the lubrication properties of metal parts. The micro-porous nature of the coating allows for better retention of oils, which can reduce friction and wear during operation.
Types of Black Oxide Coating
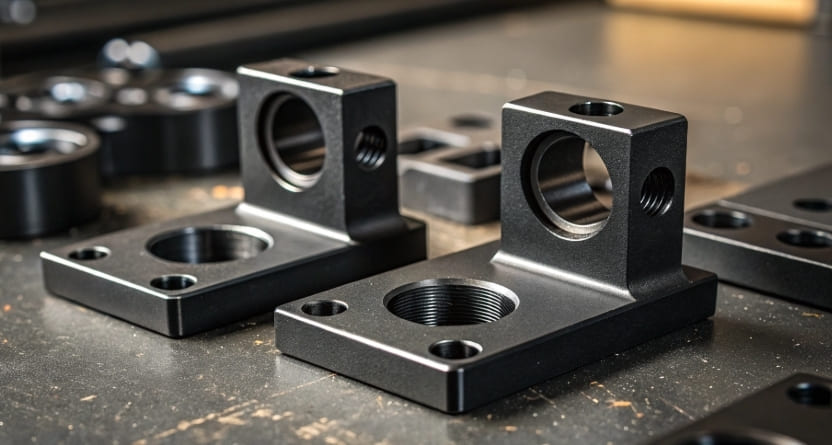
Hot Black Oxide
Hot black oxide is the most common and effective method. It involves heating the metal parts to a high temperature (typically around 285°F or 140°C) and immersing them in a hot alkaline solution. This process is suitable for a wide range of metals, including steel, cast iron, and copper.
Cold Black Oxide
Cold black oxide is a less common method that does not require heating. It involves immersing the metal parts in a room-temperature solution. While this method is faster and less energy-intensive, it may not provide the same level of corrosion resistance as hot black oxide.
Mid-Temperature Black Oxide
Mid-temperature black oxide is a newer method that operates at a temperature range of 200-220°F (93-104°C). This process offers a balance between the effectiveness of hot black oxide and the energy efficiency of cold black oxide.
Black Oxide on Aluminum
While less common, black oxide coating can also be applied to aluminum. However, the process is more complex and may require the use of additional chemicals to achieve the desired finish.
Step-by-Step Guide to Applying Black Oxide Coating
Step 1: Cleaning the Metal
- Degreasing: Use a degreaser to remove any oils or greases from the surface of the metal.
- Pickling: If necessary, use a pickling solution to remove rust and other surface contaminants.
- Rinsing: Rinse the part thoroughly with water to remove any residual chemicals.
Step 2: Applying the Black Oxide Solution
- Heating the Solution: If using hot black oxide, heat the solution to the required temperature (285°F or 140°C).
- Immersion: Carefully immerse the metal part into the black oxide solution. The immersion time will vary depending on the type of metal and the desired finish.
- Agitation: Gently agitate the part to ensure uniform coating and to prevent the formation of bubbles.
Step 3: Rinsing and Drying
- Rinsing: After the coating is applied, rinse the part with water to remove any residual chemicals.
- Drying: Dry the part using compressed air or a heat gun. It is important to dry the part quickly to prevent rusting.
Step 4: Post-Treatment (Optional)
- Oil or Wax Coating: Apply a thin layer of oil or wax to enhance the protective properties of the black oxide coating and to prevent rust.
- Inspection: Inspect the part for any defects or areas where the coating may be thin or incomplete.
Applications of Black Oxide Coating
Firearms Industry
In the firearms industry, black oxide coating is widely used to reduce glare, improve aesthetics, and provide a level of corrosion resistance. It is particularly popular for gun barrels, receivers, and other components that require a professional, non-reflective finish.
Automotive Industry
Automotive manufacturers often use black oxide coating for various parts, including engine components, brake parts, and fasteners. The coating helps to reduce wear and improve the overall appearance of these parts, making them look sleek and modern.
Aerospace Industry
Aerospace applications demand high precision and durability. Black oxide coating is used in this industry to protect components from corrosion and wear, especially in environments where exposure to moisture and chemicals is common.
Medical Industry
In the medical field, black oxide coating is used for surgical instruments and other medical devices. The coating provides a non-reflective surface that is easy to clean and sterilize, making it ideal for use in operating rooms and other clinical settings.
Other Industries
Black oxide coating is also used in the following industries:
- Tooling and Machining: For drills, taps, and other cutting tools.
- Electronics: For connectors and other components that require a non-glare finish.
- Jewelry: For a unique, dark finish on metals like silver and gold.
Factors to Consider When Using Black Oxide Finish
Before deciding to use black oxide finish on your precision machined parts, consider these factors:
Material Compatibility
Not all metals are suitable for black oxide coating. The process works best on ferrous metals like steel and cast iron. Aluminum, brass, and other non-ferrous metals may require different processes or additional steps to achieve a black oxide finish.
Pre-Treatment
Proper pre-treatment is crucial for a successful black oxide coating. The metal part must be clean and free of contaminants. This often involves degreasing, pickling, and rinsing the part before it is immersed in the black oxide solution.
Post-Treatment
After the coating is applied, the part must be rinsed and dried to prevent rusting. In some cases, an additional oil or wax coating may be applied to enhance the protective properties of the black oxide layer.
Environmental Considerations
The black oxide coating process involves the use of chemicals, which can have environmental implications. It is important to follow proper disposal and handling procedures to minimize the impact on the environment.
Common Defects and Solutions for Black Oxide Coating
Even with the best intentions, defects can occur during the black oxide process. Here are some common issues and their solutions:
- Uneven Coating: This can be caused by improper cleaning or variations in the solution. Ensure thorough cleaning and consistent solution temperature.
- Spots or Patches: These are often due to contamination or hard water. Use deionized water and maintain a clean environment.
- Poor Adhesion: If the coating doesn’t stick well, it might be due to insufficient alkaline cleaning. Increase the cleaning time or temperature.
- Excessive Wear: Black oxide is not as wear-resistant as other coatings. Consider additional treatments like oil immersion to enhance durability.
- Color Variations: Different metals can produce different shades of black. Standardize your materials or adjust the process for consistent results.
Performance Tests for Black Oxide Finish
To ensure the quality and effectiveness of your black oxide finish, several performance tests can be conducted:
- Salt Spray Test: This test measures the corrosion resistance of the coating. A black oxide finish should last at least 24 hours in a salt spray environment.
- Adhesion Test: A tape test can be used to check the adhesion of the coating. The tape is applied and then pulled off to see if any coating comes with it.
- Hardness Test: While black oxide doesn’t significantly increase hardness, it can be tested to ensure the metal’s properties haven’t been compromised.
- Visual Inspection: A simple but effective method to check for uniformity and any visible defects.
Pros and Cons of Black Oxide Finish
Like any coating, black oxide has its advantages and disadvantages. Let’s break them down:
Pros | Cons |
---|---|
Cost-Effective | Limited Corrosion Resistance |
Preserves Tolerances | Not Suitable for All Metals |
Aesthetic Appeal | Requires Additional Post-Treatment |
Reduces Glare | Can Flake or Chip |
Improves Wear Resistance | Environmental Concerns |
Comparison with Other Surface Treatments
Black Oxide vs. Paint
Feature | Black Oxide | Paint |
---|---|---|
Corrosion Resistance | Moderate | Poor |
Aesthetic Appeal | Uniform, non-reflective | Can be any color |
Wear Resistance | High | Low to moderate |
Dimensional Stability | High | Low |
Cost | Low to moderate | Moderate to high |
Lubrication Properties | Improved | Not significantly |
Black Oxide vs. Electroplating
Feature | Black Oxide | Electroplating |
---|---|---|
Corrosion Resistance | Moderate | High |
Aesthetic Appeal | Uniform, non-reflective | Can be any color |
Wear Resistance | High | High |
Dimensional Stability | High | Low to moderate |
Cost | Low to moderate | High |
Lubrication Properties | Improved | Not significantly |
Black Oxide vs. Anodizing
Feature | Black Oxide | Anodizing |
---|---|---|
Corrosion Resistance | Moderate | High |
Aesthetic Appeal | Uniform, non-reflective | Can be any color |
Wear Resistance | High | Very high |
Dimensional Stability | High | Low |
Cost | Low to moderate | Moderate to high |
Lubrication Properties | Improved | Not significantly |
Conclusion
Black oxide coating is a versatile and cost-effective solution for enhancing the appearance and durability of precision machined parts. By understanding the process, types, and applications, you can make informed decisions about whether this finish is right for your project. Always consider the factors that affect the quality of the coating and be prepared to conduct performance tests to ensure the best results. With the right approach, black oxide can significantly improve your parts and contribute to the success of your manufacturing endeavors.
I hope this guide has been helpful! If you have any more questions or need further assistance, feel free to reach out. Happy machining!
FAQs
Q1: Can black oxide be applied to non-ferrous metals?
A1: While black oxide is primarily used for ferrous metals, aluminum and some other non-ferrous metals can be blackened using specialized processes.
Q2: How long does a black oxide finish last?
A2: The lifespan of a black oxide finish depends on the environment and additional treatments. With proper care, it can last several years.
Q3: Is black oxide coating environmentally friendly?
A3: The chemicals used in black oxide processes can be harmful to the environment. Proper handling and disposal are essential to minimize environmental impact.
Q4: Can black oxide be used for decorative purposes?
A4: Yes, black oxide is often used for its aesthetic appeal, providing a uniform, matte black finish that is both professional and elegant.