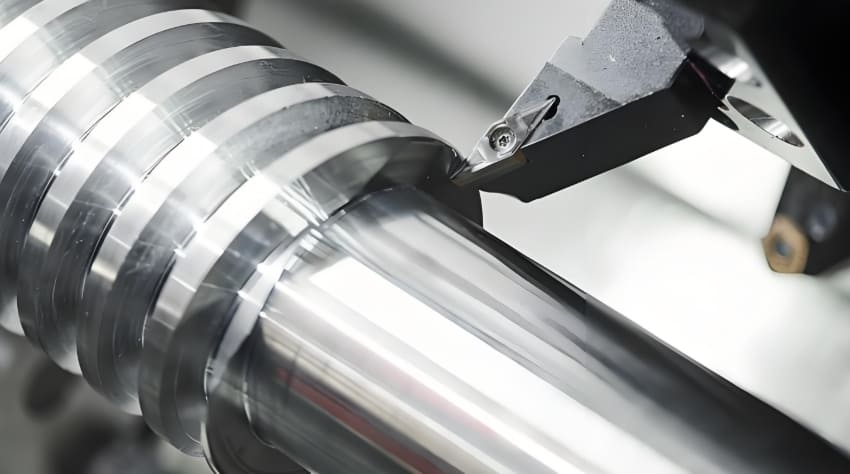
When it comes to precision and quality in manufacturing, few processes can match the capabilities of Computer Numerical Control (CNC) machining. Among the various materials used in CNC machining, stainless steel stands out for its durability, corrosion resistance, and aesthetic appeal. In this comprehensive guide, I’ll take you through everything you need to know about stainless steel CNC machining, from the basics to the advanced techniques and tools needed for success.
What is Stainless Steel CNC Machining?
Stainless steel CNC machining is a manufacturing process that uses computer-controlled machines to precisely cut, shape, and form stainless steel materials into intricate and complex parts. Unlike traditional machining methods, CNC machining relies on digital design files and automated tools to ensure high accuracy and repeatability. This process is widely used in industries where precision and performance are critical, such as aerospace, automotive, medical, and electronics.
The CNC machines used in stainless steel machining include lathes, mills, routers, and grinders. Each of these machines is equipped with a variety of cutting tools and can be programmed to perform specific tasks, from simple drilling and turning to complex multi-axis operations. The key advantage of CNC machining is its ability to produce high-quality parts with minimal human intervention, making it ideal for both prototyping and large-scale production.
Different Types of Stainless Steel for CNC Machining
Stainless steel is available in a wide range of types, each with its own unique properties and applications. Here are some of the most commonly used types of stainless steel in CNC machining:
1. Austenitic Stainless Steels
- 304 Stainless Steel: One of the most popular grades, known for its excellent corrosion resistance and formability.
- 316 Stainless Steel: Offers superior corrosion resistance, particularly in marine environments and high-temperature applications.
2. Ferritic Stainless Steels
- 430 Stainless Steel: Less expensive than austenitic grades, with good formability and moderate corrosion resistance.
- 409 Stainless Steel: Commonly used in automotive exhaust systems due to its heat resistance.
3. Martensitic Stainless Steels
- 410 Stainless Steel: Known for its high strength and hardness, often used in applications requiring wear resistance.
- 420 Stainless Steel: Similar to 410 but with even higher hardness, making it suitable for cutting tools and surgical instruments.
4. Duplex Stainless Steels
- 2205 Stainless Steel: Combines the properties of austenitic and ferritic steels, offering excellent strength and corrosion resistance.
Understanding Different Grades of Stainless Steel
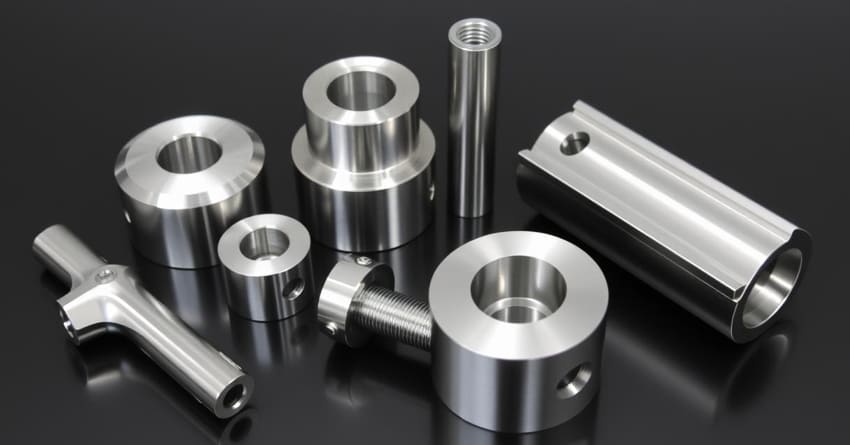
Each grade of stainless steel is designed to meet specific industrial needs. Here’s a closer look at some of the key grades:
304 Stainless Steel
- Corrosion Resistance: Excellent
- Strength: Moderate
- Formability: High
- Applications: Kitchen appliances, food processing equipment, chemical tanks
316 Stainless Steel
- Corrosion Resistance: Superior
- Strength: Moderate
- Formability: High
- Applications: Marine components, chemical processing, medical devices
430 Stainless Steel
- Corrosion Resistance: Moderate
- Strength: Low
- Formability: High
- Applications: Automotive trim, architectural panels, kitchen appliances
410 Stainless Steel
- Corrosion Resistance: Moderate
- Strength: High
- Formability: Low
- Applications: Cutting tools, surgical instruments, valves
2205 Stainless Steel
- Corrosion Resistance: Excellent
- Strength: High
- Formability: Moderate
- Applications: Marine structures, chemical processing, desalination plants
Table: Common Stainless Steel Grades and Their Properties
Grade | Type | Corrosion Resistance | Strength | Formability | Applications |
---|---|---|---|---|---|
304 | Austenitic | Excellent | Moderate | High | Kitchen appliances, food processing |
316 | Austenitic | Superior | Moderate | High | Marine components, medical devices |
430 | Ferritic | Moderate | Low | High | Automotive trim, architectural panels |
410 | Martensitic | Moderate | High | Low | Cutting tools, surgical instruments |
2205 | Duplex | Excellent | High | Moderate | Marine structures, chemical processing |
By choosing the right grade of stainless steel and applying the correct machining techniques, you can unlock the full potential of this versatile material. Whether you’re a seasoned machinist or a beginner, this guide should provide you with the knowledge you need to excel in stainless steel CNC machining.
Why Choose Stainless Steel for CNC Machining?
Stainless steel offers several advantages that make it a preferred material for CNC machining:
1. Corrosion Resistance
Stainless steel is highly resistant to corrosion, making it ideal for parts that will be exposed to harsh environments or chemicals.
2. Durability
Stainless steel is known for its toughness and ability to withstand high temperatures and mechanical stress, ensuring that parts remain reliable over time.
3. Aesthetic Appeal
The smooth, polished finish of stainless steel parts is visually appealing and can enhance the look of the final product.
4. Hygiene
Stainless steel is easy to clean and sanitize, making it a top choice for medical and food processing applications.
5. Recyclability
Stainless steel is 100% recyclable, which aligns with environmental sustainability goals.
Common Challenges and Solutions
Tool Wear
-
- Challenge: Stainless steel is a tough material that can cause rapid tool wear.
- Solution: Use high-quality, durable cutting tools and regularly inspect and replace them as needed.
Heat Generation
-
- Challenge: Machining stainless steel generates a lot of heat, which can affect the material’s properties.
- Solution: Use cooling fluids and proper cutting speeds to manage heat.
Work Hardening
-
- Challenge: Stainless steel can work harden, making it more difficult to machine as the process continues.
- Solution: Apply consistent and steady cutting forces to avoid work hardening.
Surface Finish
-
- Challenge: Achieving a smooth, polished finish can be challenging with stainless steel.
- Solution: Use fine-grit sandpaper or polishing compounds in the post-machining processes.
My Strategies for Success: Tips and Techniques
Over the years, I’ve developed a set of strategies to overcome these challenges and achieve successful stainless steel CNC machining:
- Choose the Right Grade: Selecting the most machinable grade for your application is crucial. Consider 303 for intricate parts or applications where machinability outweighs corrosion resistance.
- Use Sharp, High-Quality Tooling: Invest in carbide or high-speed steel (HSS) tools specifically designed for stainless steel. Ensure your tools are sharp to minimize work hardening and heat generation.
- Optimize Cutting Parameters: Experiment with cutting speed, feed rate, and depth of cut. Lower speeds and higher feed rates are generally recommended to reduce work hardening and heat buildup.
- Employ Effective Coolant: Coolant is essential for dissipating heat, lubricating the cutting zone, and flushing away chips. Use a high-quality coolant specifically formulated for stainless steel. Flood coolant is often preferred over mist coolant.
- Maintain Consistent Cutting: Avoid dwelling or stopping the cutting tool mid-cut, as this can lead to work hardening. Maintain a continuous cutting motion.
- Consider Climb Milling: Climb milling can sometimes improve surface finish and reduce tool wear compared to conventional milling.
- Use Rigid Workholding: Securely clamp your workpiece to prevent vibration and deflection, which can negatively impact accuracy and surface finish.
- Regular Tool Inspection: Monitor your tools for wear and replace them as needed. Dull tools are a recipe for disaster when machining stainless steel.
Tooling Recommendations and Equipments for Stainless Steel CNC Machining
To successfully machine stainless steel, you need the right tools and equipment. Here are some essentials:
1. Cutting Tools
- High-Speed Steel (HSS) Tools: Suitable for lower-speed operations.
- Carbide Tools: Ideal for high-speed machining due to their hardness and wear resistance.
- Ceramic Tools: Used for machining hard materials at very high speeds.
2. Coolants
- Water-Soluble Coolants: Effective in reducing heat and improving tool life.
- Oil-Based Coolants: Provide better lubrication and are often used for finishing operations.
3. Machine Types
- CNC Lathes: Used for turning and facing operations.
- CNC Mills: Ideal for drilling, milling, and slotting.
- CNC Routers: Suitable for cutting and shaping large, flat parts.
- CNC Grinders: Used for precision grinding and finishing.
4. Accessories
- Clamping Systems: Ensure the material is securely held in place during machining.
- Measurement Tools: Used to verify the accuracy of the machined parts.
- Finishing Tools: Help achieve the desired surface finish.
Applications of Stainless Steel CNC Machined Parts
Stainless steel CNC machining plays a vital role in several key industries:
1. Aerospace
- Applications: Engine components, fasteners, and structural parts.
- Benefits: High strength, corrosion resistance, and ability to withstand extreme temperatures.
2. Automotive
- Applications: Exhaust systems, engine parts, and trim components.
- Benefits: Durability, heat resistance, and aesthetic appeal.
3. Medical
- Applications: Surgical instruments, implants, and equipment parts.
- Benefits: Biocompatibility, ease of sterilization, and corrosion resistance.
4. Food Processing
- Applications: Food handling equipment, storage tanks, and processing machinery.
- Benefits: Hygiene, corrosion resistance, and ease of cleaning.
5. Electronics
- Applications: Enclosures, connectors, and heat sinks.
- Benefits: Precision, conductivity, and durability.
6. Chemical Processing
- Applications: Reactors, storage tanks, and piping systems.
- Benefits: Corrosion resistance, durability, and capability to handle harsh chemicals.
FAQs
1. What is the hardest type of stainless steel to machine?
Martensitic stainless steels, such as 410 and 420, are among the hardest to machine due to their high strength and hardness. However, with the right tools and techniques, these challenges can be overcome.
2. Can all types of stainless steel be CNC machined?
Yes, all types of stainless steel can be CNC machined, but the choice of tools and techniques will vary depending on the specific grade and its properties.
3. How does the cost of stainless steel CNC machining compare to other materials?
Stainless steel is generally more expensive than materials like aluminum or mild steel, both in terms of material cost and machining. However, its durability and performance often justify the higher cost.
4. What are some common post-machining processes for stainless steel parts?
Common post-machining processes include polishing, passivation, and electropolishing to improve the surface finish and enhance corrosion resistance.
5. Is stainless steel CNC machining suitable for large-scale production?
Absolutely. CNC machining is highly efficient and can be scaled up for large-scale production, ensuring consistent quality and precision.
Conclusion
Stainless steel CNC machining is a powerful tool in modern manufacturing, offering unparalleled precision and quality. Whether you’re working on a small prototype or a large production run, understanding the properties of different stainless steel grades and the challenges they present is crucial for success. With the right tools, techniques, and equipment, you can create high-performance parts that stand the test of time.