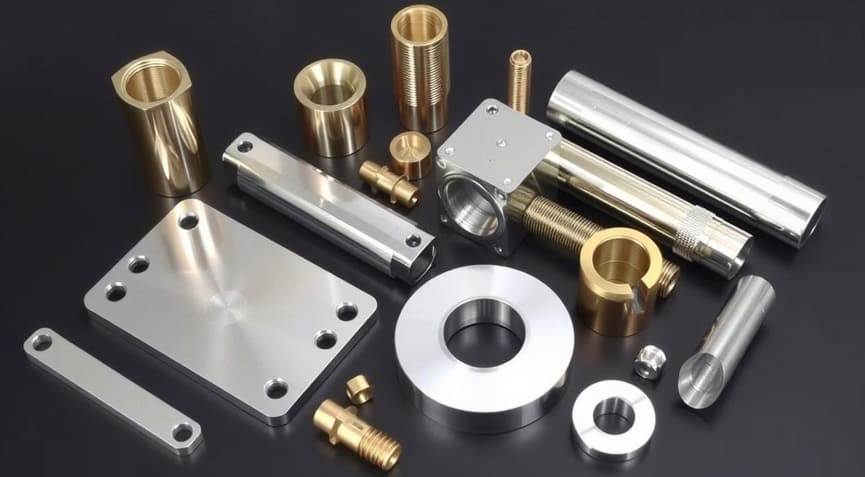
As an engineer, selecting the right metal for CNC machining is a crucial step in ensuring the success of your project. The choice of material can significantly impact the performance, durability, and cost of your final product. Whether you’re working on aerospace components, automotive parts, or intricate medical devices, understanding the properties and characteristics of various metals is essential. In this guide, I’ll walk you through the metals suitable for CNC machining, a comparison table to help you decide, and the key factors to consider when making your selection. By the end, you’ll have a solid foundation to make informed decisions that will enhance your projects.
Why Metal Selection Matters
Metal selection is not just about choosing the right material; it’s about ensuring that the material meets the specific requirements of your project. Factors such as strength, weight, corrosion resistance, thermal conductivity, and cost play a crucial role in determining the suitability of a metal for CNC machining. Selecting the wrong metal can lead to increased production costs, reduced performance, and even failure of the final product. Therefore, it’s vital to consider the following:
- Strength and Hardness: These properties determine the metal’s ability to withstand mechanical stress and wear.
- Corrosion Resistance: Essential for applications exposed to harsh environments or corrosive substances.
- Thermal Conductivity: Important for parts that need to dissipate heat efficiently.
- Machineability: The ease with which a metal can be machined without excessive wear on the tools.
- Cost: Balancing performance with budget constraints is always a priority.
- Availability: Some metals may be more readily available than others, impacting lead times and costs.
Metals Suitable for CNC Machining
1. Aluminum
Aluminum is one of the most commonly used metals in CNC machining due to its excellent machinability, lightweight, and good corrosion resistance. It’s particularly popular in the aerospace and automotive industries. Here are some common aluminum alloys used in CNC machining:
- 6061 Aluminum: This alloy is known for its good mechanical properties, weldability, and corrosion resistance. It’s ideal for general-purpose applications.
- 7075 Aluminum: This high-strength alloy is used in applications where strength and durability are critical, such as aircraft components and high-stress parts.
- 5052 Aluminum: This alloy has excellent workability and corrosion resistance, making it suitable for marine and chemical applications.
roperty | Value |
---|---|
Tensile Strength | 70-700 MPa (varies with alloy) |
Hardness (Brinell) | 15-190 HB (varies with alloy) |
Density | 2.7 g/cm³ |
Common Alloys | 6061, 7075, 5052 |
Applications | Aerospace parts, automotive components, enclosures, heat sinks |
2. Steel
Steel is a versatile and widely used metal in CNC machining, offering a range of properties depending on the specific alloy. Here are some common types of steel used in CNC machining:
- 1018 Carbon Steel: This low-carbon steel is easy to machine and has good weldability. It’s used in a variety of applications, including gears and shafts.
- 4140 Alloy Steel: This medium-carbon alloy steel has high strength and toughness, making it ideal for components that require wear resistance and durability.
- A2 Tool Steel: This high-carbon, high-chromium steel is known for its excellent wear resistance and high hardness, suitable for dies, punches, and other tooling applications.
Property | Value |
---|---|
Tensile Strength | 400-2000+ MPa (varies with alloy) |
Hardness (Brinell) | 120-700+ HB (varies with alloy) |
Density | 7.85 g/cm³ |
Common Alloys | 1018, 1045, 4140, A36 |
Applications | Structural components, gears, shafts, fasteners |
3. Stainless Steel
Stainless steel is renowned for its corrosion resistance and aesthetic appeal, making it a popular choice in many industries. Here are some common types of stainless steel used in CNC machining:
- 304 Stainless Steel: This is the most common type of stainless steel, known for its excellent corrosion resistance and ease of fabrication.
- 316 Stainless Steel: This alloy has better corrosion resistance than 304, especially in marine and chemical environments.
- 17-4 PH Stainless Steel: This precipitation-hardening stainless steel offers high strength and corrosion resistance, making it ideal for high-performance applications.
Property | Value |
---|---|
Tensile Strength | 500-1500+ MPa (varies with alloy) |
Hardness (Brinell) | 150-400+ HB (varies with alloy) |
Density | 8.0 g/cm³ |
Common Alloys | 303, 304, 316 |
Applications | Medical devices, food processing equipment, marine parts |
4. Brass
Brass is a popular choice for CNC machining due to its excellent machinability and low friction properties. It’s often used in applications that require precision and low wear, such as electrical components and jewelry.
- C36000 Free-Cutting Brass: This grade of brass is specifically designed for ease of machining and is used in a variety of applications.
- C26000 Cartridge Brass: This alloy has good strength and formability, making it suitable for components that require both durability and aesthetics.
Property | Value |
---|---|
Tensile Strength | 300-600 MPa (varies with alloy) |
Hardness (Brinell) | 50-200 HB (varies with alloy) |
Density | 8.4-8.7 g/cm³ |
Common Alloys | C36000 (Free-Cutting Brass) |
Applications | Fittings, valves, decorative parts, musical instruments |
5. Titanium
Titanium is a high-performance metal known for its excellent strength-to-weight ratio and corrosion resistance. It’s commonly used in aerospace, medical, and chemical applications.
- Grade 2 Titanium: This pure titanium grade is used in applications where good corrosion resistance and high strength are required.
- Grade 5 Titanium (Ti-6Al-4V): This alloy is the most commonly used grade of titanium, offering high strength and excellent fatigue resistance.
6. Copper and Copper Alloys
-
- Properties: Excellent electrical and thermal conductivity, good corrosion resistance.
- Applications: Electrical components, heat exchangers, and decorative items.
- Alloys: Brass, bronze, and phosphor bronze.
- Pros: High conductivity and aesthetic appeal.
- Cons: Softer than other metals, can be more prone to wear and tear.
Property | Value |
---|---|
Tensile Strength | 200-400 MPa |
Hardness (Brinell) | 35-100 HB |
Density | 8.96 g/cm³ |
Common Alloys | C11000 (Electrolytic Tough Pitch Copper) |
Applications | Electrical connectors, heat sinks, plumbing |
7. Bronze
-
- Properties: Good wear resistance, low friction, and excellent corrosion resistance.
- Applications: Bearings, bushings, and gears.
- Alloys: C954, C955, and C957.
- Pros: Ideal for applications requiring low friction and high wear resistance.
- Cons: More expensive than steel and aluminum, and can be tricky to machine.
Comparison Tables
To help you make an informed decision, here’s a comparison table of the metals mentioned above:
Material | Properties | Common Applications | Machinability (1-10) | Cost (1-10) |
---|---|---|---|---|
6061 Aluminum | Lightweight, corrosion-resistant | Aerospace, automotive, general-purpose parts | 8 | 3 |
7075 Aluminum | High strength, durable | Aircraft components, high-stress parts | 6 | 5 |
5052 Aluminum | Corrosion-resistant, workable | Marine, chemical applications | 7 | 4 |
1018 Carbon Steel | Easy to machine, good weldability | Gears, shafts, mechanical parts | 7 | 2 |
4140 Alloy Steel | High strength, toughness | Wear-resistant components, tooling | 6 | 4 |
A2 Tool Steel | High hardness, wear resistance | Dies, punches, tooling | 4 | 6 |
304 Stainless Steel | Corrosion-resistant, aesthetic | Various industries, decorative parts | 5 | 5 |
316 Stainless Steel | Superior corrosion resistance | Marine, chemical, medical applications | 5 | 6 |
17-4 PH Stainless Steel | High strength, corrosion-resistant | High-performance applications | 3 | 7 |
C36000 Free-Cutting Brass | Low friction, easy to machine | Electrical components, jewelry | 9 | 3 |
C26000 Cartridge Brass | Good strength, formable | Decorative, functional parts | 8 | 4 |
Grade 2 Titanium | Corrosion-resistant, high strength | Aerospace, medical, chemical applications | 5 | 8 |
Grade 5 Titanium (Ti-6Al-4V) | High strength, fatigue resistance | Aerospace, medical, high-performance parts | 4 | 9 |
Factors to Consider in Metal Selection
-
Project Requirements
- Strength and Durability: For high-strength applications, consider steel or titanium.
- Weight: For lightweight applications, aluminum is often the best choice.
- Corrosion Resistance: Stainless steel or titanium for environments where corrosion is a concern.
- Thermal Properties: Copper for applications requiring high thermal conductivity.
-
Machinability
- Tool Wear: Some metals, like titanium, can be abrasive and cause rapid tool wear. Use appropriate cutting tools and coolants to mitigate this.
- Surface Finish: Certain metals, like aluminum, machine to a better surface finish, which can be important for precision parts.
- Chip Formation: The type of chips produced during machining can affect the efficiency of the process. For example, aluminum tends to form long, stringy chips, while steel forms shorter, more manageable chips.
-
Post-Machining Processes
- Heat Treatment: Some metals, like tool steel, require heat treatment to achieve optimal properties.
- Surface Treatments: Coatings, plating, and anodizing can enhance the properties of the metal and improve its performance.
-
Cost and Availability
- Budget: Consider the total cost, including the price of the raw material, machining, and any post-machining processes.
- Lead Times: Some metals may have longer lead times, especially if they are not commonly stocked.
The Selection Process: A Step-by-Step Approach
Here’s a structured approach I use when selecting metals for CNC machining projects:
- Define Requirements: Clearly identify the functional, environmental, and budgetary requirements of the part.
- Consider Properties: Based on the requirements, determine the critical material properties (strength, corrosion resistance, machinability, etc.).
- Research Candidate Metals: Explore different metals and alloys that meet the required properties. Consult material data sheets and online resources.
- Evaluate Machinability: Assess the machinability of each candidate metal. Consider factors like cutting speeds, tool wear, and surface finish.
- Estimate Costs: Compare the material costs and machining costs for each candidate.
- Test and Validate: If possible, machine prototypes using different metals to validate your choice.
- Make Your Decision: Based on your analysis, select the metal that best meets your needs.
Practical Tips for Metal Selection
-
Consult with Experts
- Don’t hesitate to consult with material scientists, metallurgists, or experienced machinists. They can provide valuable insights and help you avoid common pitfalls.
-
Prototype and Test
- Before committing to a large production run, create prototypes to test the metal’s performance in real-world conditions. This can help you identify any issues early on.
-
Consider the Environment
- Think about the operating environment of your final product. For example, if it will be exposed to saltwater, choose a metal with excellent corrosion resistance like stainless steel or titanium.
-
Evaluate Tooling Costs
- Some metals, like titanium, can be more expensive to machine due to the need for specialized tools. Factor this into your overall cost analysis.
-
Sustainability
- Consider the environmental impact of your metal choice. Some metals are more sustainable and have a lower carbon footprint, which can be important for eco-friendly projects.
Case Studies
-
Aerospace Industry
- Material: Ti-6Al-4V
- Application: Aircraft components
- Rationale: Titanium’s high strength-to-weight ratio and excellent corrosion resistance make it ideal for aerospace applications where weight and durability are crucial.
-
Automotive Industry
- Material: 6061 Aluminum
- Application: Engine components
- Rationale: Aluminum’s lightweight and good machining properties make it a popular choice for automotive parts, especially in performance and racing applications.
-
Medical Industry
- Material: 316 Stainless Steel
- Application: Surgical instruments and implants
- Rationale: 316 stainless steel’s biocompatibility and corrosion resistance are essential for medical devices and implants.
FAQs
Q1: What is the best metal for CNC machining?
The best metal for CNC machining depends on the application. Aluminum is generally easy to machine and cost-effective, making it a popular choice. However, for high-performance applications, materials like titanium and stainless steel are preferred.
Q2: How do I choose a metal that balances cost and performance?
To balance cost and performance, consider the specific requirements of your application. For example, if high strength is not critical, you might opt for a more cost-effective material like 1018 Carbon Steel instead of A2 Tool Steel.
Q3: What are the advantages of using stainless steel over carbon steel?
Stainless steel offers superior corrosion resistance and a better aesthetic finish compared to carbon steel. However, carbon steel is more cost-effective and easier to machine for general-purpose applications.
Q4: Is titanium always the best choice for aerospace applications?
While titanium is highly favored in aerospace applications due to its excellent strength-to-weight ratio and corrosion resistance, it’s not always the best choice. Factors like cost, lead time, and specific project requirements should also be considered.
Q5: Can brass be used in high-precision applications?
Yes, brass can be used in high-precision applications due to its low friction properties and excellent machinability. It’s often used in electrical components and precision parts.
Conclusion
Selecting the right metal for CNC machining is a critical decision that can greatly impact the success of your project. By considering the application, evaluating machinability, assessing cost, and considering other factors like availability and post-machining processes, you can make an informed choice that meets your project’s needs. Whether you’re working with aluminum, steel, stainless steel, brass, or titanium, understanding the properties and characteristics of these materials will help you achieve the best results. Use the comparison table provided to guide your decision-making process, and don’t hesitate to consult with experts or suppliers to ensure you make the best choice for your specific requirements.
I hope this guide helps you navigate the complex world of metal selection for CNC machining. Remember, the right material can make all the difference!